神華包頭煤制烯烴升級示范項目
建設(shè)性質(zhì):改擴建
建設(shè)規(guī)模:年產(chǎn)70萬噸級聚烯烴
建設(shè)地點:內(nèi)蒙古自治區(qū)包頭市九原工業(yè)園區(qū)(現(xiàn)有工廠內(nèi)及現(xiàn)有工廠區(qū)的南側(cè),廠外灰渣場在現(xiàn)有灰渣場的西側(cè)附近)
投資:項目總投資約1715080.61萬元
建設(shè)期:建設(shè)期4年
年操作時數(shù):8000小時
生產(chǎn)制度與定員:企業(yè)的行政管理人員、高級生產(chǎn)管理人員和后勤人員按白班考慮,根據(jù)生產(chǎn)特點和生產(chǎn)運行的要求,生產(chǎn)部門按五班三運轉(zhuǎn)編制
生產(chǎn)定員:700人,全部為新增員工
項目特點
(1)采用國內(nèi)自主知識產(chǎn)權(quán)的技術(shù)方案和國產(chǎn)化大型裝備。
煤氣化擬采用先進的、國產(chǎn)化粉煤加壓氣化技術(shù),該技術(shù)具有氧耗低、煤耗低、煤種適應(yīng)性廣等一系列優(yōu)點。粉煤加壓氣化屬于氣流床氣化技術(shù),氣流床氣化單爐產(chǎn)量大、氣化效率高,適用于甲醇、醋酸、合成氨、IGCC等大型、超大型的化工裝置,也可為大型的石油化工裝置提供氫氣。甲醇制烯烴采用神華自主知識產(chǎn)權(quán)的SHMTO 技術(shù)。
(2)與現(xiàn)有工程系統(tǒng)整合,提高系統(tǒng)運行的可靠性,保證系統(tǒng)的長周期運行。
項目在現(xiàn)有工程基礎(chǔ)上擴大規(guī)模、實現(xiàn)技術(shù)升級,采用聚乙烯、聚丙烯“雙聚”方案,調(diào)整產(chǎn)品品種結(jié)構(gòu),向規(guī);、集約化發(fā)展,通過系統(tǒng)整合和系統(tǒng)調(diào)度,可以將全廠停車的“大檢修”通過不停車“小檢修”完成,通過現(xiàn)有工程和升級示范項目裝置的系統(tǒng)整合,提高系統(tǒng)的可靠性和長周期運行,符合“工業(yè)轉(zhuǎn)型升級”的要求。
(3)總結(jié)現(xiàn)有工廠的經(jīng)驗,加強運行管理的精細化管理,探索建設(shè)智慧工廠。
總結(jié)現(xiàn)有工程生產(chǎn)運行中的經(jīng)驗教訓,在環(huán)保、監(jiān)測、能效管理等方面加強精細化管理,逐步實現(xiàn)工廠運行的智能化,逐步向?qū)崿F(xiàn)智慧型工廠的轉(zhuǎn)變。
(4)項目不再新設(shè)燃煤鍋爐,采用直供電方案。
項目蒸汽平衡結(jié)合現(xiàn)有工程蒸汽使用現(xiàn)狀綜合考慮,缺少的高壓蒸汽如開車用蒸汽等,均由現(xiàn)有工程熱電中心提供。本項目工藝廢鍋副產(chǎn)的中、低壓蒸汽除滿足本項目使用外,剩余部分送至現(xiàn)有工程同等級蒸汽管網(wǎng)。工藝裝置防爆區(qū)域內(nèi)的大功率壓縮機優(yōu)先采用蒸汽驅(qū)動,非防爆區(qū)內(nèi)的壓縮機盡量采用電驅(qū)的直供電方案,不建燃煤鍋爐、汽輪發(fā)電機組和余熱發(fā)電機組。本升級示范項目建成投產(chǎn)后,將大大緩解蒙西電網(wǎng)電力負荷過剩、發(fā)電廠年運行時間低、發(fā)電廠運行負荷低的現(xiàn)狀。
(5)采用嚴格的環(huán)保標準要求。
項目不設(shè)置燃煤鍋爐,顆粒物、氮氧化物、二氧化硫等排放量遠低于同類項目;同時項目通過采用先進的生產(chǎn)工藝和采取嚴格的環(huán)保措施,最大限度地減少各項污染物排放,以滿足嚴格的環(huán)保標準要求。如本項目硫回收裝置采用先進的尾氣處理技術(shù)(克勞斯+尾氣加氫還原+堿法脫硫),排放尾氣中SO2濃度滿足《石油煉制工業(yè)污染物排放標準》(GB 31570—2015)特別排放限值(100 mg/m3)要求;同時本項目配套建設(shè)結(jié)晶分鹽設(shè)施,對現(xiàn)有工程廢水進行“控鹽提質(zhì)”升級改造,最終實現(xiàn)全廠廢水不外排。
(6)能源轉(zhuǎn)化效率高。
項目通過采取各種先進工藝和節(jié)能措施,如采用余熱回收利用、燃料氣回收和高效烯烴分離等工藝,有效地提高了本項目能源轉(zhuǎn)化效率。本項目的單位烯烴產(chǎn)品綜合能耗為2.22 噸標煤,低于2.8 噸標煤的要求,耗新鮮水為9.47 噸,低于16 噸的準入要求。本項目能源轉(zhuǎn)化效率為45.06%,滿足大于44%的準入要求。
(7)降低水資源消耗。
項目在正常工況下的生產(chǎn)廢水、生活污水和污染雨水通過廢水回用深度處理、膜濃縮蒸發(fā)結(jié)晶處理實現(xiàn)全廠廢水不外排,當本項目污水處理及回用系統(tǒng)發(fā)生運行故障和運行不穩(wěn)定等非正常工況時,利用廠內(nèi)各種緩沖儲池(罐)和現(xiàn)有工程污水處理系統(tǒng)富余處理能力進行緩沖與處理。同時通過“以新帶老”,對現(xiàn)有工程的污水處理系統(tǒng)排水進行“控鹽提質(zhì)”升級改造,將現(xiàn)有工程回用水裝置的反滲透濃水通過本項目新建的膜濃縮及蒸發(fā)結(jié)晶裝置提取鹽分、進行水質(zhì)提升處理并回用。本項目通過采取各種節(jié)水工藝和節(jié)水措施,如大量采用空冷技術(shù)、采用閉式循環(huán)水系統(tǒng)、節(jié)水消霧冷卻塔技術(shù)、采用電驅(qū)動替代蒸汽驅(qū)動和廢水回用技術(shù)等,降低了本項目水資源消耗。
(8)生化污泥資源化利用
通過將生化污泥帶水直接參與現(xiàn)有工程水煤漿制漿的方式進入氣化爐“摻燒”的方式,實現(xiàn)廠內(nèi)生化污泥的資源化利用,從而實現(xiàn)固體廢物的減量化、資源化利用。
工藝流程
原料煤先通過煤氣化生產(chǎn)出以CO和H2為主要產(chǎn)品的合成氣,其次通過一氧化碳變換、低溫甲醇洗、甲醇合成等技術(shù),將煤轉(zhuǎn)化為甲醇,再通過甲醇制烯烴技術(shù)獲得低碳烯烴,然后通過前脫丙烷后加氫的烯烴分離工藝,為下游PP、PE、MTBE/丁烯-1、C4/C5+綜合利用裝置提供原料,最后獲得聚乙烯、聚丙烯等目標產(chǎn)品。
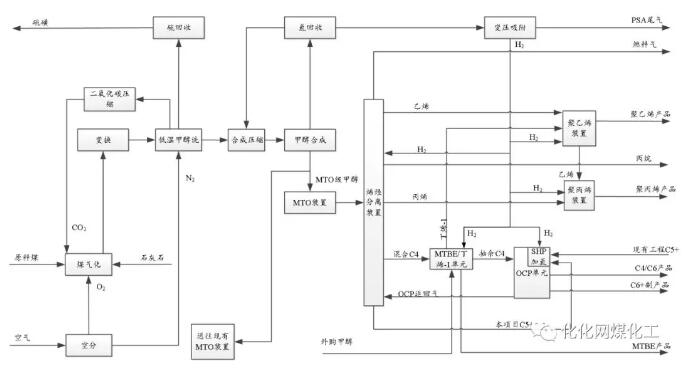
產(chǎn)品方案
項目以布爾臺煤礦、寸草塔二礦和上灣煤礦的混煤為原料采用粉煤加壓氣化工藝,經(jīng)變換、低溫甲醇洗、甲醇合成,制取200×104 t/a 甲醇(中間產(chǎn)品,100%計)。其中195.21×104 t/a 甲醇經(jīng)甲醇制烯烴裝置及烯烴分離生產(chǎn)乙烯、丙烯等中間產(chǎn)品,并進一步深加工為聚乙烯和聚丙烯。剩余甲醇送至現(xiàn)有裝置使用。主要產(chǎn)品和中間產(chǎn)品有MTO級甲醇、聚合級乙烯、聚合級丙烯、硫磺、MTBE、丁烯-1、聚丙烯、聚乙烯等。
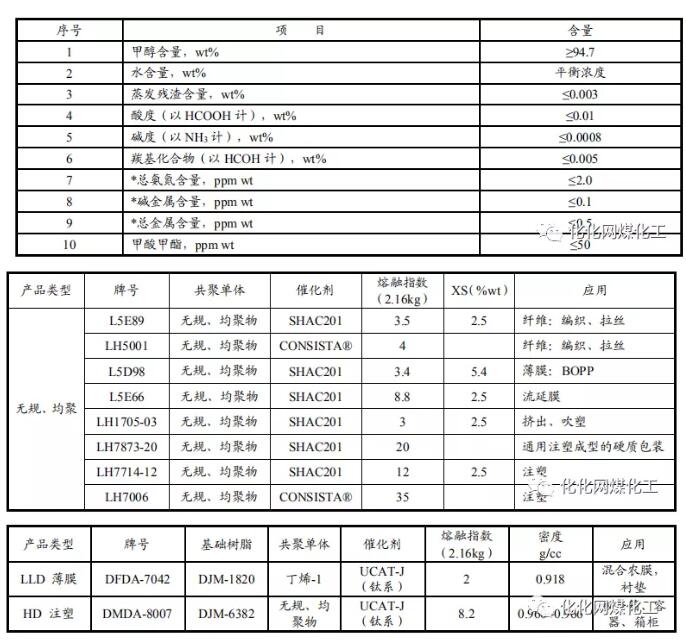
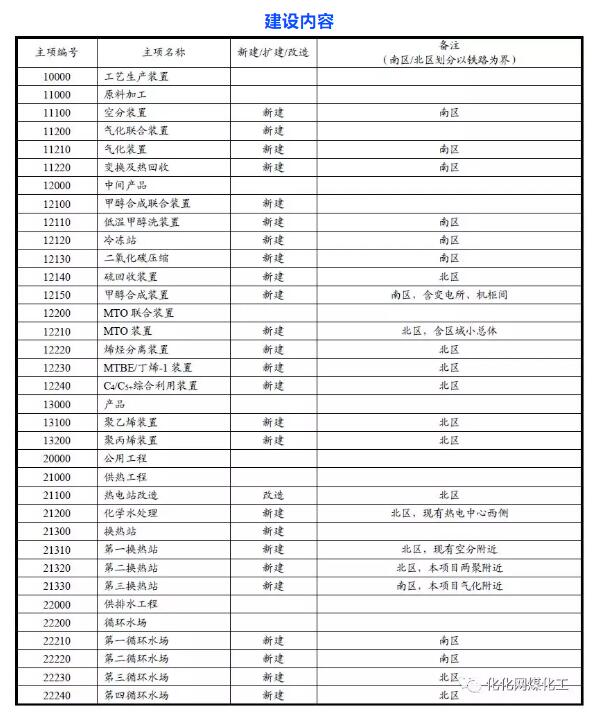
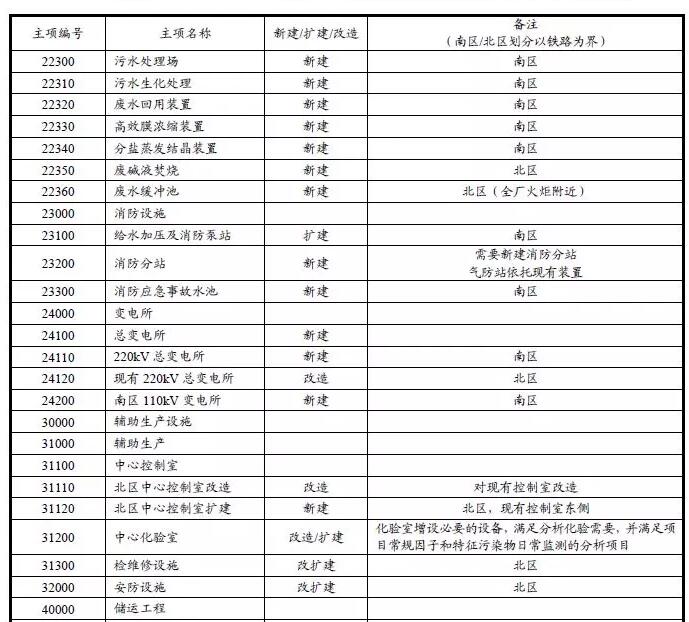
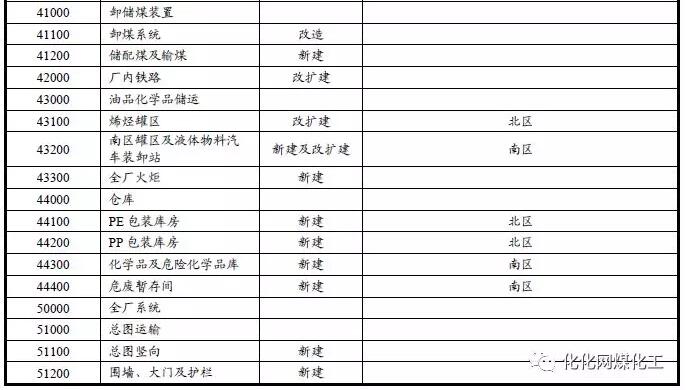
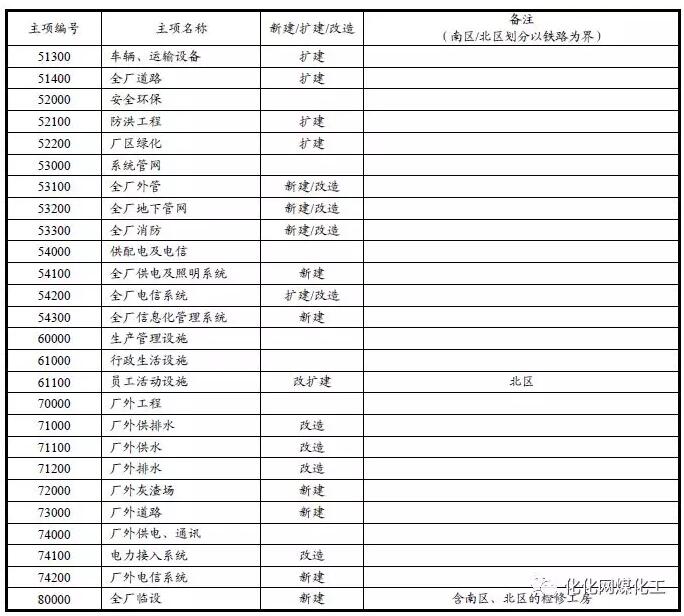
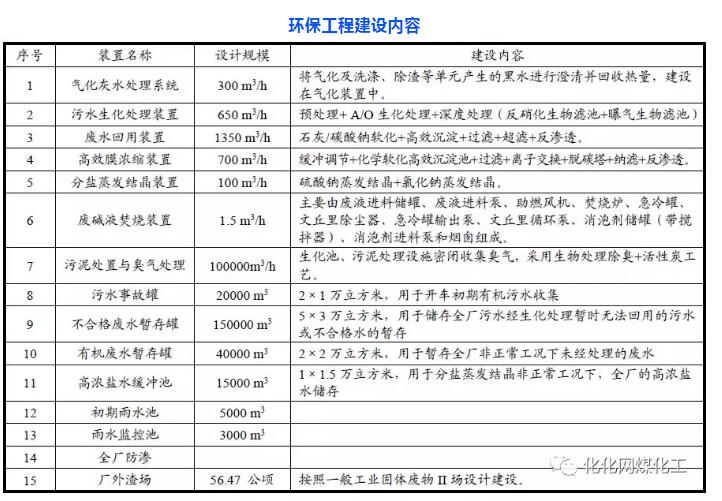