該組合水池共由5個部分組成,分別為:調(diào)節(jié)池A/B、一級RO濃水池、浸沒超濾產(chǎn)水池、RO產(chǎn)水池。池子總長100米,寬23米,高6米,總?cè)莘e13800m³。
內(nèi)蒙古寶豐煤基新材料有限公司為寧夏寶豐能源集團股份有限公司以自有資金人民幣95000萬元與其全資子公司寧夏寶豐能源集團烯烴二廠有限公司共同在內(nèi)蒙設立的子公司。項目擬以內(nèi)蒙古寶豐煤基新材料有限公司為主體,結(jié)合配套建設風光制氫一體化示范項目,實現(xiàn)綠電、綠氧、綠氫耦合碳減排基礎(chǔ)上減少外購甲醇量穩(wěn)定烯烴產(chǎn)能。
內(nèi)蒙古寶豐煤基新材料有限公司一期260萬噸/年煤制烯烴和配套40萬噸/年植入綠氫耦合制烯烴項目一期投資478億元,采用綠氫與現(xiàn)代煤化工融合協(xié)同生產(chǎn)工藝,將建成全國單廠規(guī)模最大的“綠氫+”煤制烯烴產(chǎn)業(yè)基地。
3月6日,由陜西化建工程有限責任公司承建的內(nèi)蒙古寶豐煤基新材料有限公司一期260萬噸/年煤制烯烴和配套40萬噸/年植入綠氫耦合制烯烴項目開工儀式在施工現(xiàn)場舉行。
圖片
3月1日,中國化學工程第六建設有限公司參建的內(nèi)蒙古寶豐煤基新材料有限公司一期260萬噸/年煤制烯烴和配套40萬噸/年植入綠氫耦合制烯烴項目甲醇建安工程正式開工。
項目計劃于2023年3月前將完成各項施工準備工作,項目全面開工建設,18個月建成投產(chǎn),實現(xiàn)以氫換煤、減碳增效。
2022年11月23日,生態(tài)環(huán)境部下發(fā)《關(guān)于內(nèi)蒙古寶豐煤基新材料有限公司一期260萬噸/年煤制烯烴和配套40萬噸/年植入綠氫耦合制烯烴項目環(huán)境影響報告書的批復》(環(huán)審〔2022〕183號),同意寧夏寶豐能源集團股份有限公司控股子公司內(nèi)蒙古寶豐煤基新材料有限公司在內(nèi)蒙古鄂爾多斯市烏審旗蘇格里經(jīng)濟開發(fā)區(qū)圖克工業(yè)項目區(qū)新建260萬噸/年煤制烯烴和配套40萬噸/年植入綠氫耦合制烯烴工程。
項目采用綠氫與現(xiàn)代煤化工協(xié)同生產(chǎn)工藝,烯烴總產(chǎn)能為300萬噸/年,是目前為止全球單廠規(guī)模最大的煤制烯烴,也是全球唯一一個規(guī);镁G氫替代化石能源生產(chǎn)烯烴的項目。
項目概況
內(nèi)蒙古寶豐煤基新材料有限公司為寧夏寶豐能源集團股份有限公司以自有資金人民幣95000萬元與其全資子公司寧夏寶豐能源集團烯烴二廠有限公司共同在內(nèi)蒙設立的子公司。
項目擬以內(nèi)蒙古寶豐煤基新材料有限公司為主體,結(jié)合配套建設風光制氫一體化示范項目,實現(xiàn)綠電、綠氧、綠氫耦合碳減排基礎(chǔ)上減少外購甲醇量穩(wěn)定烯烴產(chǎn)能。
項目名稱:內(nèi)蒙古寶豐煤基新材料有限公司綠氫與煤化工耦合碳減排創(chuàng)新示范項目
項目類別:根據(jù)《建設項目環(huán)境影響評價分類管理名錄(2021年版)》,本項目屬于“二十二、石油、煤炭及其他燃料加工業(yè)25”中“煤炭加工252”、“二十三、化學原料和化學制品制造業(yè)26”中“基礎(chǔ)化學原料制造261”和“合成材料制造265”
建設性質(zhì):新建
建設地點:內(nèi)蒙古自治區(qū)鄂爾多斯市烏審旗蘇里格經(jīng)濟開發(fā)區(qū)圖克工業(yè)項目區(qū)
建設單位:內(nèi)蒙古寶豐煤基新材料有限公司
占地面積:594.43公頃
全廠定員:3500人
工程總投資:報批總投資4781137萬元,其中建設投資(含增值稅)4431109萬元,建設期利息315296萬元,鋪底流動資金34732萬元。
建設規(guī)模:主要建設3×220萬噸/年甲醇裝置(含7×110000Nm3/h氧氣的空分,3×56.2萬Nm3/h有效氣(CO+H2)的氣化、變換及熱回收和低溫甲醇洗,3×6.5萬噸/年硫磺回收)、3×100萬噸/年甲醇制烯烴裝置(含烯烴分離)、3×50萬噸/年聚丙烯裝置、3×55萬噸/年聚乙烯裝置、20萬噸/年C4制1-丁烯裝置、20萬噸/年蒸汽裂解裝置。除生產(chǎn)聚丙烯和聚乙烯外,還同時副產(chǎn)硫磺、重碳四、C5+、乙烯焦油、MTBE等產(chǎn)品。
運行時間:8000小時/年
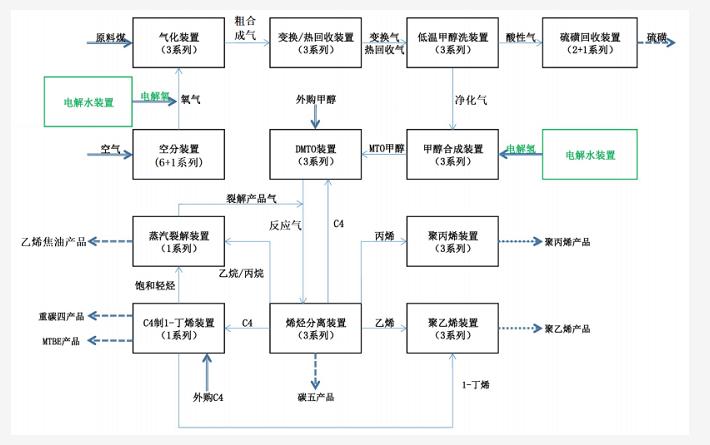
總加工流程圖
內(nèi)蒙古寶豐煤基新材料有限公司綠氫與煤化工耦合碳減排創(chuàng)新示范項目是以260萬噸/年煤制烯烴為基礎(chǔ),由配套建設的風光制氫一體化示范項目(單獨立項建設)為依托逐年補充綠氫和綠氧,補充的氫氣直接補入甲醇合成裝置,減少變換及熱回收裝置變換部分的負荷(變換是通過CO與H2O反應生產(chǎn)H2和CO2,以滿足后續(xù)甲醇合成反應所需的H2/CO比),從而減少工藝系統(tǒng)CO2的排放量;補充的氧氣作為氣化用氧,減少空分裝置負荷,從而減少燃料煤用量。在基于原料煤消耗不變的情況下,通過逐年補氫、補氧增加自產(chǎn)甲醇產(chǎn)量,至補氫第五年自產(chǎn)甲醇產(chǎn)量可滿足下游甲醇制烯烴的需求,在此同時實現(xiàn)CO2的逐年減排。本項目主體工藝為原料煤經(jīng)水煤漿加壓氣化(激冷流程)、變換、凈化后得到凈化氣,凈化氣與風光制氫一體化示范項目補充的氫氣混合作為甲醇合成的原料氣,通過低壓甲醇合成技術(shù)生產(chǎn)MTO級甲醇,再通過甲醇制烯烴技術(shù)生產(chǎn)聚合級乙烯和丙烯,聚合級乙烯、丙烯分別經(jīng)聚合得到聚乙烯、聚丙烯產(chǎn)品。為合理利用各種副產(chǎn)物料,對烯烴分離副產(chǎn)的乙烷、丙烷和C4制1-丁烯副產(chǎn)的飽和輕烴通過蒸汽裂解技術(shù)以增加乙烯、丙烯產(chǎn)量;對烯烴分離過程副產(chǎn)的混合C4通過分離得到1-丁烯,作為聚乙烯裝置生產(chǎn)原料。