高效低能耗合成尿素工藝技術(shù)
1.技術(shù)適用范圍
適用于合成氨、尿素行業(yè)節(jié)能技術(shù)改造。
2.技術(shù)原理及工藝
尿素合成的原料為液氨和CO2 氣體,液氨和CO2 在高壓下反應(yīng)先生成氨基甲酸銨(簡稱:甲銨),甲銨再經(jīng)過脫水生產(chǎn)尿素。生成甲銨和甲銨脫水生成尿素的反應(yīng)均為可逆反應(yīng),轉(zhuǎn)化率受反應(yīng)條件影響,一般不超過 75%,因此需要對未反應(yīng)物進(jìn)行分離回收,通過設(shè)置中、低壓系統(tǒng)實現(xiàn)。要生產(chǎn)顆粒尿素,需要將尿液濃縮到 96%以上才能造粒,同時為了控制副產(chǎn)物縮二脲的生成,尿液濃縮需要在真空條件下進(jìn)行操作,同時對工藝?yán)淠哼M(jìn)行處理,處理后的凈化工藝?yán)淠鹤鳛殄仩t給水回收利用。工藝流程簡圖如下:
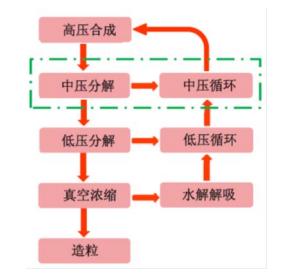
3.技術(shù)指標(biāo)
(1)噸尿素耗原料液氨 568 kg;
(2)噸尿素耗原料 CO2 735 kg;
(3)循環(huán)水耗 70t;
(4)噸尿素耗電 25 kW·h;
(5)噸尿素耗蒸汽 750kg
4.技術(shù)功能特性
(1)全冷凝反應(yīng)器提高副產(chǎn)蒸汽的品位,分級利用蒸汽及蒸汽冷凝液,降低蒸汽消耗、降低了循環(huán)冷卻水消耗;
(2)裝置投資最低,與引進(jìn)的同規(guī)模裝置相比,至少低 20%;
(3)高壓設(shè)備可以全部國產(chǎn),后期維護(hù)費用低。
5.應(yīng)用案例
山東華魯恒升化工股份有限公司肥料功能化項目。技術(shù)提供單位為中國五環(huán)工程有限公司。
(1)用戶用能情況簡單說明
改造前為傳統(tǒng)水溶液全循環(huán)法尿素裝置,由于水溶液全循環(huán)法尿素技術(shù)過于落后,所以在本案例中本技術(shù)的比較對象是傳統(tǒng) CO2 汽提法尿素工藝。傳統(tǒng) CO2 汽提法尿素工藝噸尿素蒸汽消耗約 1000kg、電耗 23 kW·h、循環(huán)水耗 75t。
(2)實施內(nèi)容及周期
置換 2 套傳統(tǒng)水溶液全循環(huán)裝置,改建 CO2壓縮機(jī)系統(tǒng)、外管廊、尿素主裝置、造粒塔、棧橋、包裝樓、變電所、機(jī)柜間、循環(huán)水站、汽車站臺和火車站臺等。
實施周期 25 個月。
(3)節(jié)能減排效果及投資回收期
改造后,噸尿素 2.4MPaG 飽和蒸汽消耗節(jié)約 250kg、電耗高 2 kW·h、循環(huán)水號低 5t。每年按滿負(fù)荷生產(chǎn)(100 萬噸),年節(jié)省蒸汽 25 萬 t、增加電耗 200 萬 kW·h、節(jié)約循環(huán)水 500萬噸,節(jié)約的中壓蒸汽減去增加的電耗折合標(biāo)煤 3.15 萬噸。
按中壓蒸汽價格為 130 元/噸,電價按 0.5 元/ kW·h 計算,循環(huán)水按 0.2 元/t 計算,年可水電汽節(jié)約費用為 3250 萬元。
該項目綜合年節(jié)能效益合計為 3250 萬元,節(jié)能改造部分總投入為 6000 萬元。投資回收期約 22 個月。
6.未來五年推廣前景及節(jié)能減排潛力
預(yù)計未來 5 年,在機(jī)床行業(yè)推廣應(yīng)用可達(dá)到 16%,可形成節(jié)能 84 萬tce/a,減排CO2 226.8 萬t/a。
一、工業(yè)節(jié)能技術(shù)部分
(一)流程工業(yè)節(jié)能改造技術(shù)
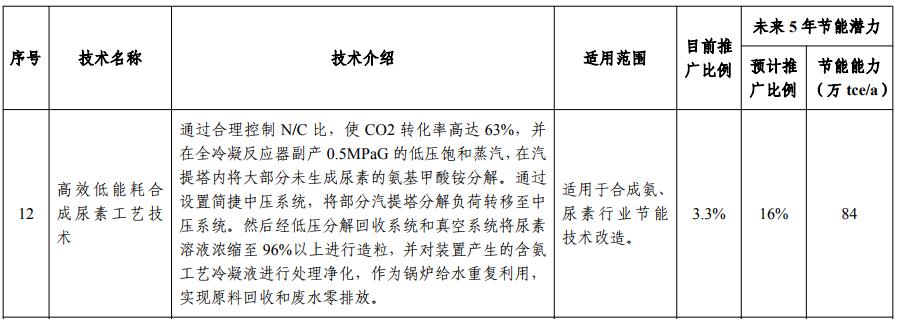
(四)可再生能源及余能利用技術(shù)
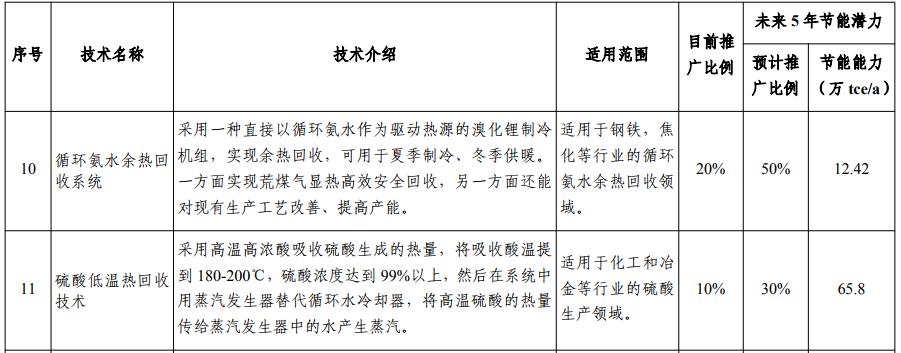