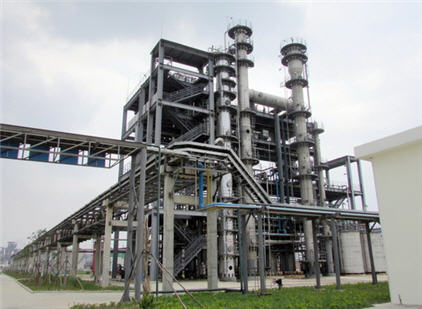
4萬噸全新工藝制H2O2工業(yè)示范裝置建成
主要技術(shù)指標(biāo)達國際同類水平 節(jié)能降耗及推廣示范意義顯著
我國大宗無機化工產(chǎn)品領(lǐng)域的過氧化氫技術(shù)研發(fā)與工業(yè)化取得重大成果。記者昨天從中國石化撫順石油化工研究院獲悉,采用該院與湖南興鵬化工科技有限公司、上海宸鵬化工科技有限公司共同開發(fā)的固定床蒽醌法生產(chǎn)H2O2成套新工藝技術(shù),在廣西自治區(qū)百色市田東縣石化工業(yè)園建設(shè)的4萬噸/年(40%)工業(yè)化示范裝置于今年3月28日一次開車成功。裝置標(biāo)定結(jié)果表明:工作液蒽醌含量180克/升、氫效10克/升,一次產(chǎn)品濃度42%、萃余平均0.14 克/升,產(chǎn)品質(zhì)量達標(biāo),各項技術(shù)指標(biāo)均達到國際同類技術(shù)水平。
據(jù)上海宸鵬化工科技有限公司傅騏介紹,過氧化氫(俗名:雙氧水)是一種重要的無機化工產(chǎn)品,因其本身無毒,使用時僅生成氧和水,對環(huán)境無污染,被稱為綠色化學(xué)品,已廣泛應(yīng)用于紡織、造紙、化工、輕工、電子、醫(yī)藥和環(huán)保等許多領(lǐng)域。世界各國對其生產(chǎn)和應(yīng)用的研究開發(fā)十分重視。目前,我國雙氧水生產(chǎn)能力約1000萬噸/年(按27.5%濃度)。我國雙氧水技術(shù)開發(fā)與生產(chǎn)始于20世紀(jì)50年代,1971年我國第一套蒽醌法生產(chǎn)雙氧水裝置問世。80年代中期前,均采用為鎳催化劑攪拌釜工藝,此后,采用鈀催化劑固定床蒽醌法工藝。目前國內(nèi)絕大部分生產(chǎn)企業(yè)均采用固定床蒽醌法工藝生產(chǎn)雙氧水。
近年來,我國雙氧水產(chǎn)能急劇增長,共50余家80余套裝置,年產(chǎn)能達到1000萬噸(按27.5%濃度),其中絕大部分采用鈀(Pd)催化劑固定床氫化工藝。到2004年底,中國的雙氧水產(chǎn)能比美國多出近35%,從而取代了美國成為全球最大的雙氧水生產(chǎn)國,但我國H2O2生產(chǎn)技術(shù)卻無較大的技術(shù)進步,只能靠簡單的機械放大來擴大單套裝置的生產(chǎn)能力。隨著中國石化陸續(xù)開發(fā)出綠色化學(xué)合成工藝——環(huán)己酮氨肟化合成己內(nèi)酰胺和雙氧水氧化丙烯制環(huán)氧丙烷等技術(shù),對雙氧水裝置的單套產(chǎn)能、安全性及節(jié)能降耗提出了更高要求。
此外,目前國內(nèi)已建有的近1000萬噸(按27.5%)H2O2裝置均采用鈀催化劑固定床工藝,工作液均采用磷酸三辛酯和重芳烴二組份溶劑體系,如采用國外技術(shù)進行技術(shù)升級,大部分設(shè)備和原材料無法利用,帶來巨大的資源浪費。鑒于此,中國石化撫順石油化工研究院、湖南興鵬化工、上海宸鵬化工緊密合作,在多年研發(fā)的基礎(chǔ)上,成功開發(fā)出了固定床蒽醌法制H2O2成套新工藝技術(shù),整套技術(shù)既可用于新裝置建設(shè),也可適用現(xiàn)有裝置改造。
6月5日,撫順石化南寧研究院主持召開雙氧水生產(chǎn)新工藝成套技術(shù)及工業(yè)應(yīng)用現(xiàn)場研討會。
據(jù)撫順石化研究院學(xué)術(shù)委員會成員、工程部主任、教授級高工齊慧敏介紹,固定床蒽醌法生產(chǎn)H2O2成套新工藝技術(shù),由全酸性環(huán)境運行、新型復(fù)配工作液體系、新型高活性和選擇性催化劑體系、新型關(guān)鍵塔設(shè)備及內(nèi)構(gòu)件技術(shù)四部分組成,具有安全性能高、副反應(yīng)少、能耗物耗低、投資省、成本低等優(yōu)點。該技術(shù)及15萬噸/年雙氧水(50%)裝置工藝包已于2012年7月通過了中國石化集團總部的技術(shù)評議,專家一致認為:開發(fā)的固定床雙氧水制備新工藝安全可靠、反應(yīng)效率高,工藝包設(shè)計指標(biāo)先進,氫效、物耗、能耗等重要技術(shù)指標(biāo)達到國際同類技術(shù)水平,整體技術(shù)具有創(chuàng)新性和自主運作權(quán),建議推進工業(yè)化轉(zhuǎn)化。
該成套新工藝技術(shù),與國內(nèi)現(xiàn)有裝置的工藝相比:在同樣工作液流量下,裝置產(chǎn)能可提高30%;一次產(chǎn)品濃度比原來高7%;催化劑用量是原工藝的1/3,減少催化劑投資1/2;工作液反應(yīng)載體溶解度增加,同等氫化度下,氫效可達10克/升,單位體積工作液生產(chǎn)效率提高35%;同規(guī)模主生產(chǎn)裝置設(shè)備管路投資減少20%,投資可降低20%;氧化反應(yīng)時間縮短、萃取效率提高,可產(chǎn)>40%濃度產(chǎn)品;產(chǎn)品能耗降低15%、綜合成本可下降50元/噸(按27.5%濃度產(chǎn)品計),具有十分可觀的節(jié)能降耗效果和推廣示范意義。
據(jù)介紹,該成套技術(shù)的創(chuàng)新點之一是開發(fā)成功了全新酸性工作液循環(huán)生產(chǎn)體系,消除了原工藝用堿處理存在的安全隱患,為裝置大型化提供安全保障;創(chuàng)新點之二是新型復(fù)配工作液體系,即將H2O2生產(chǎn)中的加氫載體-蒽醌溶解于重芳烴、磷酸三辛酯(TOP)和2-甲基環(huán)己基醋酸酯(2-MCHA)中組成的工作液,改變并優(yōu)化工作液組成,提高工作液中有效蒽醌的含量,提高氫效和裝置的產(chǎn)能,為裝置大型化提供產(chǎn)能保證;創(chuàng)新點之三是開發(fā)出了新型高活性和選擇性SC-A06催化劑,新開發(fā)成功的這種新型鈀/氧化鋁催化劑(專利號:ZL2011 1,0276795.5),與國內(nèi)現(xiàn)有裝置普遍使用的催化劑比較,大量減少了催化劑的用量。以目前在設(shè)計中的中國石化長嶺分公司30萬噸(27.5%濃度)H2O2項目為例,使用國內(nèi)原有催化劑需用催化劑110噸左右,而新催化劑僅需30噸;創(chuàng)新點之四是開發(fā)成功了新型高效關(guān)鍵塔設(shè)備及內(nèi)構(gòu)件技術(shù)(CN201120349651.3、CN201120556541.4、CN201120556539.7、CN201220549474.8),包括先進的氫化塔結(jié)構(gòu),可使加氫反應(yīng)在溫和適宜的條件下進行,減少副反應(yīng)的發(fā)生,特殊的氧化反應(yīng)與分離一體化氧化塔結(jié)構(gòu),大大提高了工作液和氧化尾氣的分離效率、氧化塔的操作彈性和安全性,高效氣液傳質(zhì)填料,提高氧化收率至95%以上,高效復(fù)合型萃取塔結(jié)構(gòu)設(shè)計,提高篩板效率30%以上。
來自廣東、福州的客戶,到裝置施工現(xiàn)場考察,了解該項目的建設(shè)情況。
湖南興鵬化工科技有限公司卿光宗在接受記者采訪介紹,湖南興鵬化工科技有限公司和上海宸鵬化工科技有限公司自籌資金6000余萬投資建設(shè)的4萬噸/年(40%)H2O2工業(yè)化裝置,其建成投產(chǎn)和正常的運行表明,其具有重要的工業(yè)化推廣與示范意義。若采用該成套技術(shù)建設(shè)H2O2工業(yè)化裝置,單套裝置產(chǎn)能可達40萬噸/年(按27.5%),國家計劃推廣的過氧化氫法制環(huán)氧丙烷一般規(guī)模為30萬噸,需配套80萬噸H2O2年(27.5%),建二套裝置可滿足需求,而使用現(xiàn)有技術(shù)需建5套以上才能滿足需求,因此新技術(shù)使大規(guī)模新環(huán)氧丙烷工藝技術(shù)推廣有了可行的配套技術(shù),且投資、占地均大幅減少。
目前,國內(nèi)現(xiàn)有技術(shù)生產(chǎn)H2O2能力達1000萬(27.5%)噸/年,如全部用此技術(shù)改造可增加產(chǎn)能300萬噸,降低成本達4億,降低電耗3億度。由于產(chǎn)品濃度高,在使用過程中可減少原料水用量25%,大量節(jié)省用水及廢水處理費用。對于新建裝置,以目前新建10萬噸(按27.5%)H2O2裝置為例:用新技術(shù)比采用傳統(tǒng)技術(shù)投資降低了2000萬,年生產(chǎn)成本降低500萬。而對于原生產(chǎn)裝置進行改造,也以10萬噸(27.5%)H2O2裝置為例僅需增加1000多萬投資就能增產(chǎn)近3萬噸(27.5%)產(chǎn)能,噸產(chǎn)品成本下降50元,即年增加利稅600多萬。
據(jù)了解,目前我國第一套雙氧水法10萬噸/年生產(chǎn)環(huán)氧丙烷工業(yè)試驗裝置已采用該成套新工藝技術(shù),并配套建設(shè)15萬噸(50%濃度,相當(dāng)于30萬噸27.5%濃度)H2O2裝置。該聯(lián)合裝置計劃于2014年5月30日前在中國石化長嶺分公司建成投產(chǎn)。