[摘 要]通過(guò)與當(dāng)前國(guó)際合成塔技術(shù)進(jìn)行比較,介紹了ⅢJD系統(tǒng)及內(nèi)件技術(shù)的設(shè)計(jì)思想,內(nèi)件的結(jié)構(gòu)特性及優(yōu)點(diǎn),ⅢJD技術(shù)的推廣應(yīng)用情況等。
[關(guān)鍵詞]氨合成;內(nèi)件;技術(shù)
0 前言
氨是最為重要的基礎(chǔ)化工產(chǎn)品之一,其產(chǎn)量居各種化工產(chǎn)品的首位。合成氨同時(shí)也是能源消耗的大戶,世界上大約有10%的能源用于生產(chǎn)合成氨。我國(guó)為合成氨生產(chǎn)大國(guó),擁有超過(guò)500家的大、中、小型合成氨企業(yè)。但就單套系統(tǒng)的產(chǎn)量而言,均無(wú)法和國(guó)外的單套系統(tǒng)、單產(chǎn)量相比,近年來(lái),國(guó)內(nèi)的合成氨企業(yè)能力不斷擴(kuò)大,大家都向著“大型化、低能耗、清潔生產(chǎn)、長(zhǎng)周期運(yùn)行”方向發(fā)展,由此整合著我國(guó)合成氨生產(chǎn)資源的分配,也分配著能源。
湖南安淳高新技術(shù)有限公司從事合成氨工業(yè)技術(shù)的開(kāi)發(fā)和節(jié)能型氨合成系統(tǒng)技術(shù)研究20多年,在全國(guó)合成氨行業(yè)率先開(kāi)發(fā)了31.4MPa壓力級(jí)的DN1200、DN1400、DN1600、DN1800、DN2000、DN2200系統(tǒng)。目前正在進(jìn)行更大型化低壓合成技術(shù)的開(kāi)發(fā)和多級(jí)合成系統(tǒng)的工程實(shí)施。正在推進(jìn)著單套合成氨裝置大型化和高產(chǎn)化的國(guó)產(chǎn)化進(jìn)程,將我國(guó)的合成氨技術(shù)和世界合成氨先進(jìn)技術(shù)“接軌”,開(kāi)發(fā)了與我國(guó)合成氨造氣方法和造氣水平相配套、有中國(guó)特色的合成氨技術(shù)。特別是氨合成系統(tǒng)及合成反應(yīng)器內(nèi)件的設(shè)計(jì),從系統(tǒng)流程的設(shè)置、各工藝設(shè)備的設(shè)計(jì)等方面“獨(dú)辟溪徑”,創(chuàng)造了多項(xiàng)專利及專有技術(shù)。
目前,安淳公司配套和設(shè)計(jì)的合成系統(tǒng),單套合成氨能力達(dá)1000 t/d,近期將投產(chǎn)運(yùn)行。筆者作為技術(shù)參與者,下面對(duì)我公司利用獨(dú)有的專利技術(shù)開(kāi)發(fā)的氨合成系統(tǒng)及氨塔反應(yīng)器內(nèi)件進(jìn)行介紹。
1 國(guó)外合成氨技術(shù)的現(xiàn)狀和進(jìn)展
1.1 70年代至90年代的氨合成技術(shù)回顧
國(guó)外著名的合成氨技術(shù)及產(chǎn)品供應(yīng)商有英國(guó)ICl、德國(guó)Uhde、德國(guó)Braun公司、德國(guó)Linde公司、丹麥Topsφe、美國(guó)Kellogg等公司。在合成氨系統(tǒng)全套工藝技術(shù)開(kāi)發(fā)和氨合成塔及合成塔高壓回路上,相繼開(kāi)發(fā)出各具特色的工藝技術(shù)。具有大型化、系列化、能源綜合利用科學(xué)化等諸多優(yōu)點(diǎn)。其中有很多不乏為經(jīng)典之作。
我國(guó)合成氨工業(yè)進(jìn)入大型化是從上世紀(jì)70年代開(kāi)始的,當(dāng)時(shí)國(guó)家在經(jīng)濟(jì)十分困難的條件下引進(jìn)了13套合成氨裝置,引進(jìn)的裝置涵蓋上述各個(gè)公司的技術(shù),可以稱之為集當(dāng)時(shí)國(guó)際上合成氨新技術(shù)之大全。
當(dāng)時(shí),氨合成反應(yīng)器最具有代表性的為Kellogg公司的“K”型氨合成塔,該塔為四床或三床全冷激式塔;再有Braun公司的二塔或三塔氨合成系統(tǒng),Braun流程中三個(gè)合成塔均為絕熱層塔,第一合成塔出口配置工藝氣加熱器,第二和第三合成塔出口安裝有廢熱鍋爐,回收合成塔出口反應(yīng)氣熱量,產(chǎn)生高壓蒸汽(13.03MPa、溫度331℃);還有Uhde公司的三床全徑向型(第三徑向床出口無(wú)換熱器)氨合成塔,Lurgi公司的二床全徑向型合成塔等塔型。當(dāng)時(shí)國(guó)際國(guó)內(nèi)的大型合成氨裝置大部分為立式塔型。我國(guó)引進(jìn)合成氨裝置中以Kellogg公司的冷激式氨合成塔較多,這種大型的塔(180 kt/a,15MPa合成回路壓力,DN3200的塔型)以塔直徑大、催化劑裝填量多、運(yùn)行的“空速”小等方式來(lái)實(shí)現(xiàn)高產(chǎn)量。
著名的Braun流程和合成塔則采用三個(gè)立式的絕熱型催化劑筐,每個(gè)塔外設(shè)換熱器或蒸汽過(guò)熱器對(duì)反應(yīng)氣降溫和回收反應(yīng)熱,這也是用較多的催化劑來(lái)實(shí)現(xiàn)較高的氨凈值,進(jìn)而減少循環(huán)量和提高熱回收率的方法,也為簡(jiǎn)化合成塔反應(yīng)器結(jié)構(gòu)、提高熱回收率、提高氨凈值等創(chuàng)造了一種經(jīng)典的流程及設(shè)計(jì)思路。
1.2 90年代以來(lái)氨合成技術(shù)的發(fā)展及思維走向
進(jìn)入90年代以來(lái),隨著能源的緊張,也隨著新技術(shù)新材料的不斷出現(xiàn),各個(gè)著名合成氨公司又從新材料、及新型催化劑入手,創(chuàng)造了更加完美的新型流程和氨合成反應(yīng)器。具有代表性的低能耗制氨工藝有4種:Kellogg公司的KREP工藝、Braun公司的低能耗深冷凈化工藝、UHDE-ICI-AMV工藝、Topsφe工藝和S-200、S-50型氨合成塔及S-250型的串塔工藝;也有Uhde公司大能力的三塔雙級(jí)壓力氨合成圈流程及三床均為徑向流的合成塔,這種流程及配合的雙級(jí)壓力回路最高日產(chǎn)達(dá)到了3300t;另外還有KBR流程和臥式橫向流氨合成塔;還有一直堅(jiān)持采用軸徑向流合成塔工藝的Casale合成塔及流程。
這些公司對(duì)合成塔及合成回路流程的改進(jìn),都是在大型化、降低回路及氨合成塔塔阻力降、徑向流的設(shè)置等方面開(kāi)展工作。輔以采用新型催化劑,使合成回路的運(yùn)行效率更高、熱回收量更多、回收的蒸汽品位更高。同時(shí)單系統(tǒng)的產(chǎn)量也遂步上升,目前最大氨合成回路的單套生產(chǎn)能力達(dá)3300t/d以上。
總結(jié)來(lái)看,主要從下述幾方面著手進(jìn)行技術(shù)革新。
① 從全系統(tǒng)(從造氣崗位開(kāi)始至合成氨工序)著手,開(kāi)發(fā)系統(tǒng)總能耗低的制氨工藝技術(shù)。主要以節(jié)能降耗為目的,立足于改進(jìn)和發(fā)展工藝單元技術(shù)。
② 注重凈化技術(shù),創(chuàng)造進(jìn)入合成高壓圈氣體凈化度高、惰氣含量少的反應(yīng)氣氣源。諸如采用低溫甲醇洗串深冷凈化工藝、分子篩凈化工藝等技術(shù)。
③ 注重降低回路阻力,也更注重采用小顆粒催化劑和廣泛采用徑向流技術(shù),提高氨凈值、減少循環(huán)量和提高熱回收率。
④ 隨著機(jī)械制造技術(shù)和材料技術(shù)水平的提高,在氨合成回路的壓力級(jí)選擇上,也不一味地降低氨合成回路的工作壓力。各公司結(jié)合合成氨總體流程,開(kāi)發(fā)了有11MPa壓力級(jí)的氨合成工序,也有14.8MPa、19.5MPa、21MPa等壓力級(jí)的合成工序。如Uhde公司采用了兩個(gè)不同壓力級(jí)進(jìn)行組合的回路技術(shù),最高級(jí)的回路工作壓力達(dá)到了21MPa。
⑤ 采用多塔串聯(lián)的方式來(lái)提高回路產(chǎn)量。由于受運(yùn)輸及制造水平等限制,合成塔大到一定尺寸后,制造成本和運(yùn)輸價(jià)格將顯著上升。為了提高回路產(chǎn)量,使裝置特大型化,運(yùn)用了多種串塔的流程。這些有傳統(tǒng)的Braun三塔或雙塔串聯(lián)流程,也有Topsφe公司的S-250型流程,這種流程是在S-200合成塔反應(yīng)器后串上一個(gè)S-50的合成塔,每反應(yīng)器配上相應(yīng)的熱回收系統(tǒng),組成串聯(lián)塔回路,更加精妙的設(shè)計(jì)組合有德國(guó)Uhde公司的雙壓力級(jí)、三塔串聯(lián)流程及合成塔技術(shù)。上述流程及塔型均可達(dá)到回路產(chǎn)量在2000t/d以上,最高已經(jīng)達(dá)到3300t/d的水平。
⑥采用釕基催化劑提高合成效率。這是為提高系統(tǒng)產(chǎn)量進(jìn)行的革命性工作,使合成塔的氨凈值提高,采用各種新型催化劑,特別是釕基型催化劑,氨凈值比傳統(tǒng)的催化劑提高5%以上。
⑦ 利用燃?xì)馔钙胶驼羝钙阶鳛閯?dòng)力的離心式壓縮機(jī)和離心式循環(huán)機(jī),有效地整合和利用工藝及原料系統(tǒng)的動(dòng)力,進(jìn)而降低整個(gè)合成氨系統(tǒng)的綜合能耗。
⑧ 提高裝置生產(chǎn)運(yùn)轉(zhuǎn)率、延長(zhǎng)運(yùn)行周期。包括工藝優(yōu)化技術(shù)、先進(jìn)的控制技術(shù)和控制手段等技術(shù)的使用。
⑨ 大型化、集成化、自動(dòng)化,使系統(tǒng)具有經(jīng)濟(jì)規(guī)模,成為低能耗與環(huán)境更友好的合成氨裝置。
通過(guò)采用上述改造思路,前期引進(jìn)的合成氨裝置,在原料路線和動(dòng)力路線上也進(jìn)行了新技術(shù)改造工作,特別是在合成氨回路及氨合成塔的改造方面下了大的力氣,基本上將原來(lái)的Kellogg全軸向冷激型氨合成塔改造成徑向流和段間換熱型,有效地降低了回路阻力,提高了產(chǎn)量,節(jié)約了能耗。
2 我國(guó)合成氨工業(yè)的現(xiàn)狀及特定工藝條件
我國(guó)引進(jìn)的大型合成氨廠總的生產(chǎn)能力僅占合全國(guó)合成氨總能力的1/4左右,其余產(chǎn)量靠幾百家中小合成氨廠來(lái)生產(chǎn),由于受原料和工藝路線的限制,能耗相對(duì)較高。
我國(guó)中小合成氨廠絕大部分以煤焦為原料。造氣工藝幾乎全部為UGI爐型的造氣工藝,系統(tǒng)后續(xù)工藝的配套大部分為銅洗凈化精制、31.4MPa壓力級(jí)的氨合成回路,這樣就構(gòu)成了我國(guó)合成氨工業(yè)大部分廠家的特定工藝條件。由于我國(guó)資源的限制,我們長(zhǎng)期面對(duì)的現(xiàn)實(shí)是以煤為原料的合成氨廠技術(shù)改造如何做,達(dá)到什么技術(shù)水平和能耗水平。
當(dāng)然,如果均用水煤漿制氣或粉煤制氣,凈化和壓縮等工序?qū)⑦M(jìn)行配套改造,這要投入大量的資金,顯然,在近期是不可能大面積實(shí)現(xiàn)的。
由于大部分廠家采用31.4MPa壓力級(jí)的合成工藝,受壓縮機(jī)的限制,裝置增產(chǎn)也必須沿著原來(lái)的特定工藝條件進(jìn)行。這樣,氨合成工段的改造在一個(gè)相當(dāng)長(zhǎng)的時(shí)間內(nèi),也必須在這種特有的工藝環(huán)境下進(jìn)行。
3 ⅢJD系列氨合成系統(tǒng)設(shè)計(jì)思想
ⅢJD系列大直徑、高產(chǎn)量型氨合成技術(shù)是湖南安淳高新技術(shù)有限公司在總結(jié)ⅢJ系列系統(tǒng)及氨合成塔內(nèi)件在全國(guó)合成氨行業(yè)400多臺(tái)套運(yùn)行經(jīng)驗(yàn)的基礎(chǔ)上,汲取90年代以來(lái)國(guó)際先進(jìn)技術(shù)以及國(guó)內(nèi)引進(jìn)的大型氨廠合成塔運(yùn)行經(jīng)驗(yàn),開(kāi)發(fā)設(shè)計(jì)的新技術(shù)。
本技術(shù)主要立足于我國(guó)現(xiàn)行的合成氨工業(yè)條件,依據(jù)我國(guó)的合成氨相關(guān)設(shè)備、相關(guān)材料及相關(guān)催化劑條件開(kāi)發(fā)的。隨著合成氨工業(yè)的發(fā)展,本技術(shù)也在“與時(shí)俱進(jìn)”,目前已經(jīng)發(fā)展到日產(chǎn)合成氨能力超過(guò)1000t,采用較高的合成塔出口溫度,使回收的蒸汽壓力更高、生產(chǎn)能力更大,系統(tǒng)運(yùn)行壓力低壓化,也進(jìn)行多塔串聯(lián)等。其內(nèi)容和形式上有別于國(guó)外的同類型工藝,這些技術(shù)完全是有自主知識(shí)產(chǎn)權(quán)、立足于國(guó)內(nèi)現(xiàn)成工藝的技術(shù)。在行業(yè)中運(yùn)用取得了較好的效果。
氨合成反應(yīng)是一個(gè)在有催化劑存在、高溫、高壓可逆的放熱反應(yīng),理論上生成1mol氨,合成反應(yīng)放熱量在450℃時(shí)可達(dá)到54.4 kmol;由于受催化劑反應(yīng)活性及平衡等因素影響,生產(chǎn)過(guò)程中采用了氣體循環(huán)生產(chǎn)的方法,為提高系統(tǒng)回收氨的水平,運(yùn)用了冷凍降溫和低溫分氨的方式。因而,合成氨系統(tǒng)可以視為一個(gè)集反應(yīng)、換熱、冷凍、分離、系統(tǒng)動(dòng)力循環(huán)多單元的系統(tǒng)。
最理想化的狀態(tài)是要求盡量多回收反應(yīng)熱,少用冷凍量、多回收冷量及熱量,盡量減少循環(huán)量。要達(dá)到這些優(yōu)化條件,設(shè)置好系統(tǒng)流程及設(shè)計(jì)好系統(tǒng)工藝條件最為關(guān)鍵。3.1 ⅢJD氨合成系統(tǒng)的基本流程(圖1)
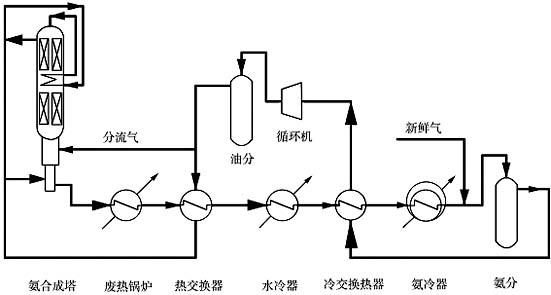
圖1 ⅢJD氨合成系統(tǒng)流程
流程敘述:從循環(huán)機(jī)來(lái)經(jīng)過(guò)氨分離后的合成循環(huán)氣再經(jīng)過(guò)循環(huán)機(jī)出口油分離器分離油滴后,氣體分成兩路:一路直接進(jìn)入合成塔的環(huán)隙,對(duì)合成塔的外殼進(jìn)行冷卻,以保護(hù)合成塔外殼,免超溫導(dǎo)致高壓條件下材料的“氫蝕”,保證合成塔的運(yùn)行安全;另一路進(jìn)入合成塔外的熱交換器,和合成塔反應(yīng)后經(jīng)過(guò)廢鍋的氣體換熱,加熱合成塔入塔氣。加熱后的氣體經(jīng)合成塔下部換熱器后進(jìn)入合成塔上層“零米”層,與段間換熱器來(lái)的氣體溫合進(jìn)入催化劑床進(jìn)行反應(yīng),經(jīng)一段、二段反應(yīng)后進(jìn)入第三段,這一段為一個(gè)間接換熱型的徑向反應(yīng)段,經(jīng)過(guò)此段反應(yīng)后再進(jìn)入絕熱的第四段反應(yīng),經(jīng)下部換熱器出塔。另一股調(diào)溫用氣是和經(jīng)過(guò)合成塔環(huán)隙的冷氣匯合,這股氣體首先從合成塔上部出來(lái),再與熱交換器出來(lái)的熱氣進(jìn)行混合,組成的混合氣再進(jìn)入合成塔的段間換熱器,調(diào)節(jié)合成塔第三段的溫度,然后進(jìn)入合成塔“零米”層。這股氣與經(jīng)過(guò)合成塔內(nèi)下部換熱器換熱出來(lái)的氣體一道進(jìn)入催化劑床反應(yīng);出合成塔后的氣體,依次進(jìn)入設(shè)置在塔外的廢熱鍋爐、熱交換器管內(nèi),與未反應(yīng)循環(huán)氣換熱,再進(jìn)入水冷卻器管內(nèi)進(jìn)行冷卻。冷卻后氣體進(jìn)入冷交換器管間,與氨冷來(lái)的冷循環(huán)氣冷熱交換后,氣體得到了比水冷更進(jìn)一步的冷卻,冷卻后的氣體再在冷交的下部分離段進(jìn)行分離,分離掉70%以上的液氨。分離后的氣體出冷交換器后進(jìn)入氨冷卻器管間(如為二級(jí)氨冷器,則串聯(lián)逐級(jí)進(jìn)行冷卻),氨冷后的氣體和壓縮來(lái)的新鮮氣混合(如果用分子篩進(jìn)行新鮮氣處理,補(bǔ)氣可以直接進(jìn)入氨合成塔)再進(jìn)入氨分離器再次分離液氨;氨分后氣體再進(jìn)入冷交換器管內(nèi),與反應(yīng)后的循環(huán)氣換熱后進(jìn)入循環(huán)機(jī)系統(tǒng)補(bǔ)壓循環(huán),這樣就完成了一個(gè)氣體循環(huán)過(guò)程。循環(huán)氣中積累的CH4、Ar等惰性氣體在水冷的一次出口處弛放,以保證循環(huán)氣中惰氣含量在控制指標(biāo)內(nèi)。
按上述流程進(jìn)行分析,我們將合成系統(tǒng)按功能分為四個(gè)單元。第一個(gè)單元為反應(yīng)器單元,這里利用ⅢJD高效氨合成反應(yīng)器來(lái)實(shí)現(xiàn)氨合成,本身進(jìn)行系統(tǒng)內(nèi)部反應(yīng)熱平衡,達(dá)到高的氨凈值、低的循環(huán)量運(yùn)行之目的,反應(yīng)效率是否能提高、催化劑利用率是否高均與本反應(yīng)器內(nèi)件的設(shè)計(jì)水平有關(guān)。第二個(gè)單元為熱回收單元,本單元的主要目的是將合成反應(yīng)熱盡可能地在廢熱鍋爐和熱交換器得到回收,達(dá)到多生產(chǎn)高品位蒸汽的同時(shí),將相對(duì)低位能的熱量加以回收,以保證合成塔自身的熱平衡,并使反應(yīng)后循環(huán)氣進(jìn)入水冷卻器的溫度最低。第三個(gè)單元為冷回收單元,本單元兩個(gè)功能,第一個(gè)功能是將合成氨的循環(huán)氣進(jìn)行冷凍,達(dá)到相應(yīng)條件下循環(huán)氣的液氨分離量最大,也就是說(shuō)達(dá)到進(jìn)入氨合成塔的入口氨含量盡量低,另一功能是將液氨氣化而產(chǎn)生的冷量進(jìn)行回收,保證冷量在冷交部分回收得盡量多,以減少氨冷器加入冷凍劑(液氨)的量,確保出冷交換器的冷氣溫度盡量高一點(diǎn),這樣冷量就得到極大的回收,減少了加入液氨的量,節(jié)約了冰機(jī)電耗。第四單元是分離單元,這個(gè)單元主要是油、水的分離和液氨的分離。如果分離效果好,將減少無(wú)用功的消耗,達(dá)到節(jié)能之目的。
3.2 反應(yīng)單元——氨合成塔反應(yīng)器
好的合成塔內(nèi)件,必須具備有能方便地實(shí)現(xiàn)設(shè)計(jì)要求的產(chǎn)量、運(yùn)行中調(diào)節(jié)掌控溫度方便、催化劑利用率高、操作彈性好、催化劑易還原、催化劑易裝卸、結(jié)構(gòu)可靠且簡(jiǎn)單、合成塔的阻力也應(yīng)盡量小。這些因素組合在一起,有的是相對(duì)立的,怎樣辯證地思考問(wèn)題,這是合成塔設(shè)計(jì)者要面對(duì)的問(wèn)題。
怎樣才能兼顧各方面,盡量?jī)?yōu)化反應(yīng)器,設(shè)計(jì)出一個(gè)在一定條件下運(yùn)行最穩(wěn)定、能量最節(jié)約的合成塔反應(yīng)器,我們經(jīng)過(guò)了近20年的不懈努力,開(kāi)發(fā)了獲得國(guó)家科技進(jìn)步二等獎(jiǎng)的系列合成塔技術(shù)及產(chǎn)品,上世紀(jì)80年代中期開(kāi)始,從小型塔入手,DN600、DN800、DN1000、DN1200、DN1400、DN1600、DN1800、DN2000、DN2200系列技術(shù)逐步發(fā)展,到目前形成了具備全系列、多規(guī)格、各種不同要求及不同系統(tǒng)條件相配套的系列合成塔技術(shù)及產(chǎn)品。
這種大型合成塔技術(shù)及反應(yīng)器,我們稱之為ⅢJD系列氨合成塔技術(shù)。這些技術(shù)在合成塔內(nèi)件反應(yīng)器設(shè)計(jì)上具備有下述特征及技術(shù)特點(diǎn)。
(1)采用分流工藝調(diào)節(jié)催化劑床層溫度
眾所周知,氨合成塔的設(shè)計(jì)是采用了適用催化劑特性的設(shè)計(jì)方法來(lái)進(jìn)行工藝及結(jié)構(gòu)設(shè)計(jì)的,而催化劑反應(yīng)達(dá)到一定的溫度后就必須將反應(yīng)熱移出,使氣體再一次以低的溫度進(jìn)入床層反應(yīng),達(dá)到第二次反應(yīng)的條件,這將進(jìn)行反復(fù)升降溫操作,使反應(yīng)沿著催化劑最適宜溫度曲線行走,才能達(dá)到盡可能高的合成塔出口氨含量,得到盡可能高的氨凈值。
經(jīng)典的合成塔工藝調(diào)溫方式有下述三種方式,見(jiàn)圖2。
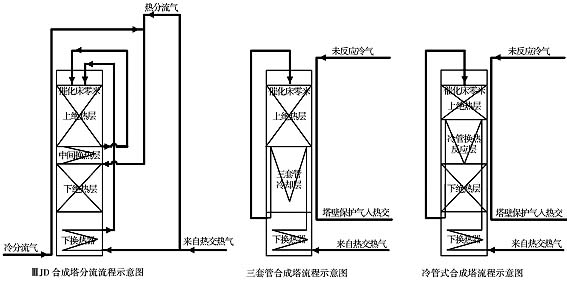
圖2 合成塔的調(diào)溫方式
大部分間接換熱式合成塔和冷管型合成塔,采用的是未反應(yīng)氣體一次性進(jìn)入。氣體在反應(yīng)前先通過(guò)管道進(jìn)入需要降溫的催化劑床層,用溫度相對(duì)較低的未反應(yīng)氣來(lái)冷卻催化劑床層的高溫段。這些合成塔有諸如傳統(tǒng)的三套管式、段間冷卻型等塔型。這種調(diào)溫方式的優(yōu)點(diǎn)是調(diào)節(jié)溫度十分簡(jiǎn)單,只在合成塔進(jìn)氣的主閥加上一個(gè)調(diào)節(jié)“零米”溫度用的副閥就可以了。在具體生產(chǎn)中,只要調(diào)節(jié)系統(tǒng)的循環(huán)量就可以方便地調(diào)節(jié)合成塔溫度了。其缺點(diǎn)是換熱管要密布在催化劑床層,進(jìn)入的氣體要反復(fù)加熱,熱氣的流程長(zhǎng)、通道窄、造成阻力大。另一方面,冷卻管內(nèi)與管外的催化劑反應(yīng)溫度差將越來(lái)越小,換熱推動(dòng)力也越來(lái)越小,造成要布置較多的管或較大的循環(huán)量來(lái)降溫的態(tài)勢(shì),這就直接導(dǎo)致了催化劑床層阻力大、催化劑裝填量小,系統(tǒng)循環(huán)量大,氨凈值提不高。采用段間降溫的方式,也有同類的問(wèn)題,同時(shí)催化劑床層設(shè)計(jì)也十分復(fù)雜。
ⅢJ系列氨合成塔則沿用了間接降溫的方式,并將內(nèi)部換熱器進(jìn)行優(yōu)化改良設(shè)計(jì)。采用冷氣體從外部引入,直接進(jìn)入不同的床層,按要求控制進(jìn)入氣量的大小、調(diào)節(jié)進(jìn)入氣體的溫度,以此來(lái)調(diào)節(jié)催化劑各床層溫度,達(dá)到了既采用間接換熱式調(diào)溫,又運(yùn)用了“冷激式”塔的“分流”、分區(qū)分層調(diào)節(jié)的優(yōu)點(diǎn)。
由于外來(lái)的“分流氣”進(jìn)入合成塔床層時(shí)的溫度較低,傳熱溫差將變得較大,這樣,內(nèi)置的段間換熱器及有關(guān)調(diào)溫元件就可設(shè)計(jì)得較小,占據(jù)的合成塔催化劑空間也較小。達(dá)到了提高催化劑裝填量、降低阻力的要求;另外,由于氣體進(jìn)行分流,也使得各催化劑床層的調(diào)節(jié)可以達(dá)到“隨心所欲”——按不同催化劑反應(yīng)活性和不同的溫度及產(chǎn)量分配流量,從而十分方便地調(diào)節(jié)催化劑各床層溫度。
這種“分流”帶來(lái)了下列好處:一是極大地降低了系統(tǒng)的循環(huán)量;二是可以使調(diào)節(jié)十分方便;三是可以使催化劑升溫還原時(shí),完全斷掉層間換熱器的氣流,創(chuàng)造一個(gè)絕熱升溫還原的條件,使催化劑還原能夠十分徹底;四是由于“分流”,一部分氣體不經(jīng)過(guò)下部換熱器,下部換熱器的管間流量相對(duì)較小,進(jìn)入中心管的氣量也較小,可減少下?lián)Q熱器的面積,也減少了氣體流動(dòng)的阻力。
這種塔內(nèi)部的分流,還只是一種分流方式。為了更加優(yōu)化系統(tǒng),我們也開(kāi)發(fā)了“全分流”的流程——冷氣進(jìn)入合成塔前進(jìn)行分流,熱氣也在進(jìn)塔前分流。成功地將進(jìn)入合成塔環(huán)隙的氣體流量下降到僅占主氣流量的10%,這樣既保證了合成塔塔壁溫度不超標(biāo),也使得合成塔環(huán)隙流的阻力大大下降。這也是ⅢJD合成塔技術(shù)一個(gè)十分顯著的特點(diǎn)。
(2)盡量不用和少用冷激方式來(lái)調(diào)節(jié)床層溫度
氣固反應(yīng)床的氨合成塔反應(yīng)器,一般都采用內(nèi)置式催化劑床層的降溫方式。不管目前的內(nèi)件設(shè)計(jì)如何千變?nèi)f化,但就其降溫的方法和降溫的原理來(lái)分有下列三種降溫方式:冷管式降溫、冷激式降溫和段間換熱器型的間接降溫方式。見(jiàn)圖3。
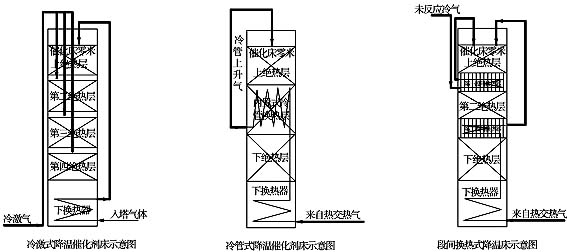
圖3 氨合成塔的降溫方式
三種降溫方式各有優(yōu)缺點(diǎn),唯有冷激式降溫方式最為簡(jiǎn)單, 但這種方式由于采用未反應(yīng)的氣體通過(guò)外分配方式進(jìn)入不同的催化劑床層,直接將反應(yīng)后升高了氣體溫度降下來(lái)的方式調(diào)溫,這樣也沖稀了反應(yīng)氣的氨濃度,當(dāng)床層設(shè)計(jì)的催化劑段數(shù)比較多時(shí),越進(jìn)入下部,這一部分未反應(yīng)氣走過(guò)的催化劑床層就越短,和催化劑接觸的時(shí)間就越少,總體來(lái)說(shuō),就會(huì)對(duì)反應(yīng)氨凈值的提高有影響。同一產(chǎn)量下,冷激式比間接換熱式的合成塔將要增加循環(huán)量,也要減少熱回收量。上世紀(jì)70年代,我國(guó)引進(jìn)的300 kt/a合成氨裝置,較多地采用Kellogg公司的瓶式多層冷激式合成塔,隨著技術(shù)的深入,迄至今日,幾乎全部改成了段間換熱型的改良“K型”塔。這樣,既提高了氨凈值,又提高了合成塔的產(chǎn)量。目前國(guó)外的Uhde公司、Topsφe公司、KBR公司、Casale公司均很少用冷激式降溫的方式來(lái)調(diào)節(jié)床層溫度,這也是隨著節(jié)能工作深入,工藝之必然選擇!
ⅢJD型合成塔內(nèi)件的降溫采用分體式,在催化床層中含有一到兩件段間換熱器組件,組成了一個(gè)四段或五段軸徑向型的合成塔。它幾乎沒(méi)有用冷激來(lái)降溫,這樣,可以達(dá)到十分好的調(diào)溫效果,同時(shí),得到盡量高的出口氨含量,盡量小的系統(tǒng)循環(huán)量。
(3)采用多氣室徑向床技術(shù)
采用徑向床,是當(dāng)前合成塔為了降低阻力降常用的方法。國(guó)外的各種塔型氣體內(nèi)部流動(dòng)方式不是采用徑向流就是采用橫向流,全部采用軸向流的塔型十分少見(jiàn)了。隨著合成塔進(jìn)入大型化,各合成塔設(shè)計(jì)公司均注重研究徑向筐的分布等問(wèn)題,做了大量的工作。我公司經(jīng)過(guò)大量的研究和工程實(shí)踐,開(kāi)發(fā)了一種多氣室、反復(fù)混合型的徑向筐分布器,這種分布器可以將徑向流的氣體在進(jìn)入氣室前經(jīng)分氣端及收氣端的初步分氣后,再在收氣端進(jìn)入多氣室反復(fù)混流型徑向分布器中,將氣體進(jìn)行多次折流、多次混合,各方向來(lái)的工藝氣體混合完全,分布均勻。
采用這種徑向筐技術(shù)后,合成塔反應(yīng)器內(nèi)約占70%以上的催化劑層氣體流動(dòng)為徑向流,反應(yīng)床層阻力降不超過(guò)0.4MPa,達(dá)到了國(guó)內(nèi)外同類合成塔的先進(jìn)水平。也達(dá)到了分氣均勻,運(yùn)行平穩(wěn)的目的。
(4)運(yùn)用可徑向流的段間換熱器技術(shù)
傳統(tǒng)的三套管和冷管式的合成塔最大阻力段均在冷管層,因冷管占據(jù)了催化劑有效截面,且高溫反應(yīng)后的氣體在冷管內(nèi)進(jìn)行了節(jié)流,因而這部分的阻力大,這是冷管式合成塔無(wú)法解決的問(wèn)題。一般來(lái)說(shuō),當(dāng)合成塔的高徑比為1/10,合成塔負(fù)荷達(dá)設(shè)計(jì)負(fù)荷時(shí),一個(gè)三套管合成塔催化劑床層的阻力降可達(dá)到1.8MPa,一個(gè)冷管式純軸向的合成塔阻力降最少也有1.2MPa,這樣就限制了合成塔大型化生產(chǎn)技術(shù)的發(fā)展,因而,冷管式合成塔基本沒(méi)有大型的塔存在。
ⅢJD型氨合成塔運(yùn)用了一個(gè)類似于冷管結(jié)構(gòu)的新型段間換熱器(已獲得了國(guó)家專利),它也是段間換熱器和冷管變形的換熱器,將它埋在催化劑床層,催化劑床的反應(yīng)氣體是沿徑向流動(dòng)的,換熱器內(nèi)作為冷卻的氣體也是沿徑向流動(dòng),與外部氣體并流進(jìn)行換熱。這就徹底解決了冷管式或換熱器式層間冷卻器無(wú)法實(shí)現(xiàn)徑向流的問(wèn)題。它和典型的段間換熱比,有管外能填充催化劑,提高反應(yīng)效率的優(yōu)勢(shì),當(dāng)然也提高了催化劑的裝填量。和傳統(tǒng)的冷管式換熱器相比,它有徑向流的優(yōu)勢(shì)。
通過(guò)這種技術(shù)的運(yùn)用,我們開(kāi)發(fā)的合成塔塔徑由DN1200上升到DN2200以上,合成塔的總阻力降均在0.4MPa以下。
(5)采用細(xì)長(zhǎng)型分列式內(nèi)部換熱器
合成塔的下部換熱器一般來(lái)說(shuō)面積較小,大直徑的塔設(shè)成一個(gè)鼓形換熱器將會(huì)使管內(nèi)的氣體流程太短,換熱效果不好,管外采用折流板時(shí),將會(huì)使換熱時(shí)氣體流動(dòng)“死區(qū)”太多,也極大地影響了換熱效率。ⅢJD采用了細(xì)長(zhǎng)形的換熱器,它和中心管設(shè)計(jì)成一個(gè)整體,這樣既便于維修,也便于提高換熱器的換熱效率,還有利于合成塔下部徑向段的設(shè)計(jì)(將徑向分氣與收氣、換熱器結(jié)合成一個(gè)整體)。細(xì)長(zhǎng)形的換熱器也更進(jìn)一步簡(jiǎn)化了內(nèi)件結(jié)構(gòu),使內(nèi)件的維修變得更加方便。
(6)采用多層復(fù)合保溫技術(shù)
多層復(fù)合式保溫技術(shù)是湖南安淳高新技術(shù)有限公司的一個(gè)專利技術(shù),它借用了航空技術(shù)及般天材料,將內(nèi)件的保溫層做得更加精致,保溫效果更好。這種技術(shù)在我公司開(kāi)發(fā)DN600合成塔就使用了,之后不斷完善,到目前為止,從未出現(xiàn)過(guò)內(nèi)件保溫層脫落而影響生產(chǎn)的情況。而這在以前,保溫層脫落是合成塔常出現(xiàn)的故障之一。
對(duì)保溫層的設(shè)計(jì),我們還對(duì)合成塔內(nèi)的反應(yīng)機(jī)理進(jìn)行了研究,考慮了對(duì)流、幅射等的影響,運(yùn)用了多種高科技的手段進(jìn)行保溫效果模擬和保溫優(yōu)化設(shè)計(jì),采用了多節(jié)式多伸縮結(jié)構(gòu)的保溫皮來(lái)保證內(nèi)件的熱脹條件好。
(7)采用連續(xù)催化劑床、催化劑自卸技術(shù)
采用了連續(xù)的催化劑床層,這也是保證自卸催化劑順暢的一個(gè)必要方式。內(nèi)件設(shè)計(jì)二到三個(gè)徑向段,每段之間的分層均采用活動(dòng)和中間有催化劑流動(dòng)孔的設(shè)計(jì)部件,完全能保證催化劑從上而下順利進(jìn)入內(nèi)件中,也保證了徑向筐上部催化劑能“封住”進(jìn)氣通道,保證徑向?qū)舆M(jìn)氣和出氣均不短路。這種設(shè)計(jì),使內(nèi)件裝配和檢修變得更加容易。
優(yōu)化設(shè)計(jì)的ⅢJD氨合成塔反應(yīng)器由一個(gè)獨(dú)立、下部帶換熱器的中心管及換熱器組件加上一個(gè)能實(shí)現(xiàn)徑向流的段間換熱器組成的活動(dòng)換熱件,和一個(gè)固定的帶有三個(gè)徑向筐的催化劑組合成的四段式、軸徑向、工藝進(jìn)氣全分流、催化劑床連續(xù)、自卸催化劑的氨合成反應(yīng)器。這種塔型也可以結(jié)合工藝的不同需要及用戶的不同情況進(jìn)行三段或四段床設(shè)計(jì),二段或三段徑向床變形設(shè)計(jì)。
內(nèi)件見(jiàn)圖4。
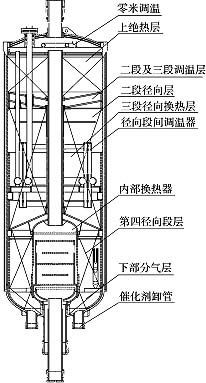
圖4 ⅢJD合成塔結(jié)構(gòu)示意
3.3 熱回收單元
ⅢJD合成工序的所謂熱回收單元由合成塔出口的廢熱鍋爐、熱交換器等組成。這個(gè)單元包含有兩臺(tái)換熱設(shè)備和幾根高溫管線。當(dāng)設(shè)計(jì)要生產(chǎn)高壓蒸汽時(shí),將設(shè)置蒸汽過(guò)熱器,這也是大型合成技術(shù)用得較多的熱回收方法。
我們?cè)谶@部分主要是運(yùn)用了一個(gè)“全分流”的流程,首先將熱交換器的冷端溫差加大,較好地保證了換熱器在換熱面積足夠的條件下,進(jìn)入水冷卻器的循環(huán)氣溫度低。一個(gè)合成系統(tǒng)進(jìn)入水冷的溫度越低,也就是說(shuō)合成塔在保證熱平衡的條件下,進(jìn)入水冷的溫度越低,則合成塔外的廢熱鍋爐回收的熱量就越多,熱量回收就越好。
(1)“全分流”的流程
“全分流”流程是ⅢJ系氨合成系統(tǒng)流程的一個(gè)特色,所謂全分流,即在冷氣入塔時(shí)進(jìn)行分流,出熱交換器的熱氣入塔前也進(jìn)行分流,進(jìn)入合成塔反應(yīng)器內(nèi)件的氣體同樣進(jìn)行分流。
圖5為分流與不分流的流程比較圖。
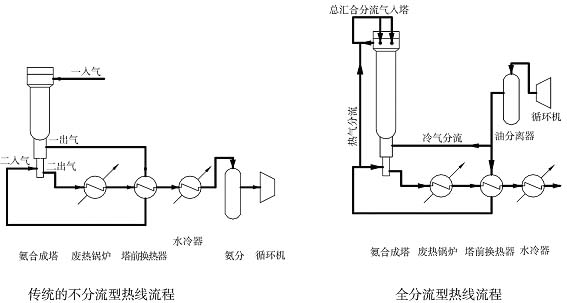
圖5 分流與不分流的流程示意
從圖5可以看出,不分流的流程中冷卻合成塔環(huán)隙是用100%的入塔氣進(jìn)入合成塔內(nèi)件和外殼之間的環(huán)隙,這樣就有一進(jìn)和一出氣體,一出氣體由于經(jīng)過(guò)了合成塔環(huán)隙,將反應(yīng)層的溫度傳遞給了一出氣,一般來(lái)說(shuō),一出氣的溫度高達(dá)60℃以上。這股氣體將合成塔反應(yīng)熱的高位能熱吸收了,變成了低位能熱。這樣,進(jìn)入熱交換器的入口氣也比從一進(jìn)來(lái)的氣要高30℃以上,勢(shì)必將會(huì)使進(jìn)入水冷卻器的反應(yīng)氣在同樣換熱器、同樣冷端溫差條件下提高30℃,也可以認(rèn)為少回收了熱量,即少產(chǎn)了蒸汽。
而“全分流”的流程僅只有10%左右的未反應(yīng)冷氣經(jīng)塔內(nèi)外筒環(huán)隙進(jìn)冷管,約90%的未反應(yīng)冷氣進(jìn)入熱交。其優(yōu)點(diǎn)是催化劑筐壁散失的熱量仍回收到催化劑筐床層內(nèi),相當(dāng)于減少了催化劑筐的熱損失。
這股10%左右的“分流氣”是保護(hù)合成塔壁的,使合成塔的塔壁溫度在適當(dāng)范圍,也不能降得太低,因?yàn)闇囟冉档锰土,高位能熱將損失太大;塔壁溫度過(guò)高了,筒體材料不能抗氫蝕,會(huì)影響運(yùn)行安全。我們將這個(gè)溫度控制在適當(dāng)?shù)姆秶鷥?nèi),這樣既挖掘了設(shè)備的運(yùn)行潛力,又不使高位能熱向低位能無(wú)謂地轉(zhuǎn)化;另一方面,這股10%的冷卻環(huán)隙氣并沒(méi)有浪費(fèi),我們的流程是將這股氣通過(guò)與熱分流氣混合后再次進(jìn)入合成塔內(nèi),作為段間換熱器的冷卻用氣,這樣做到了能量的充分利用。
這種流程,進(jìn)熱交的冷氣溫度在35~40℃,結(jié)果可使進(jìn)水冷排熱氣溫度降到80℃以下,提高了熱回收率,減少了設(shè)備投資(節(jié)省了一個(gè)軟水加熱器)。傳統(tǒng)流程中,如果不設(shè)軟水加熱器,進(jìn)冷排溫度為120~130℃。
(2)“亞熱壁”或“熱壁”合成塔
如果采用提高合成塔熱回收蒸汽壓力的方式來(lái)回收合成塔熱量,這樣,就會(huì)有一個(gè)隨著蒸汽壓力的提高,熱量逐步后移的過(guò)程。如表1所示,隨著蒸汽壓力的提高,出廢熱鍋爐的循環(huán)氣溫度將上升,進(jìn)入熱交換器的總熱量也增多,合成塔熱氣進(jìn)口溫度也將上升,合成塔內(nèi)的熱平衡也將變化,這樣也要調(diào)整出合成塔反應(yīng)器的出口溫度來(lái)達(dá)到合成塔回收熱量的效果。也會(huì)帶來(lái)合成塔的環(huán)隙溫度升高,從上述的“全分流”流程來(lái)看,也會(huì)使合成塔的塔壁溫度有所調(diào)整。
表1 ⅢJD流程中的幾種不同蒸汽壓力下系統(tǒng)溫度表
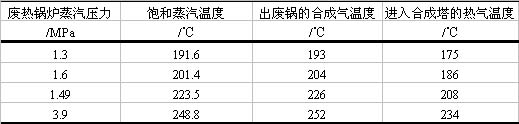
注:①依據(jù)ⅢJD流程中的設(shè)備及有關(guān)通用的設(shè)計(jì)條件來(lái)來(lái)計(jì)算;②均按廢鍋出口溫差3℃來(lái)計(jì)算,按熱交換器熱段溫差18℃來(lái)計(jì)算。
從表1可以看出,如果按回收蒸汽壓力為3.9MPa,則采用一次進(jìn)入合成塔的熱氣溫度將會(huì)達(dá)到234℃,我們采用來(lái)熱壁操作方式是將10%的冷氣進(jìn)入合成環(huán)隙,將合成塔環(huán)隙的溫度最高點(diǎn)控制在200℃以內(nèi),這就是我們稱之為“亞熱壁”的操作方式,這樣可以極大地簡(jiǎn)化工藝流程,提高熱回收的品位和熱回收率。ⅢJD合成塔大直徑反應(yīng)器,也有采用230℃塔壁溫度的,由此來(lái)回收高壓蒸汽。我們?yōu)樯綎|瑞星化工設(shè)計(jì)的日產(chǎn)800t合成氨系統(tǒng)就是用這種設(shè)計(jì)理念進(jìn)行設(shè)計(jì)的。
(3)高效換熱型設(shè)備
在有先進(jìn)按熱能位高低回收熱量流程的條件下,ⅢJD系統(tǒng)還采用了高效的熱回收技術(shù)。以此來(lái)回收合成塔出口的反應(yīng)熱,用于自身熱平衡,這主要體現(xiàn)在廢熱鍋爐和合成塔內(nèi)外熱交換器的設(shè)備設(shè)計(jì)上。
塔外的廢熱鍋爐,我們采用降低阻力的設(shè)計(jì)方法,采用了直通式或U型管式的廢熱鍋爐回收合成塔反應(yīng)熱,在布管上和設(shè)備設(shè)計(jì)上,采用了盡量降低阻力的設(shè)計(jì)方法,提高了廢熱鍋爐的熱回收效率。
塔內(nèi)熱交換器我們采用了如前所述的細(xì)長(zhǎng)形換熱器,以及高效化的換熱管,提高了換熱器的傳熱效率;塔外換熱器的設(shè)計(jì),我們也采用了高效的橫紋管換熱技術(shù),分段采用不同材料以抗蝕,極大地降低了高壓容器的設(shè)備投資。同樣條件下,同樣的傳熱量,采用這種配套技術(shù),使高壓容器的投資下降近20%。
3.4 冷回收單元
氨合成反應(yīng)器的轉(zhuǎn)化率一般在20%以下,生產(chǎn)中要采用循環(huán)反應(yīng)的方式,收集產(chǎn)品液氨方式為冷卻和冷凍分離兩種方式串聯(lián)。因氨的物化性質(zhì)決定,僅采用水冷卻方式是不能使出口氨含量達(dá)經(jīng)濟(jì)運(yùn)行水平的,工藝生產(chǎn)中采用了利用自身生產(chǎn)的液氨作為冷凍劑來(lái)冷凍合成循環(huán)氣的方式,達(dá)到將合成塔進(jìn)口循環(huán)氣氨含量控制在3%以下的指標(biāo)。
回收和利用好冷凍量,也是高壓回路的一個(gè)重要問(wèn)題。一般來(lái)說(shuō),我們要求經(jīng)過(guò)“冷回收”后的循環(huán)氣以盡量高一點(diǎn)的溫度進(jìn)入下一個(gè)設(shè)備。每生產(chǎn)1噸產(chǎn)品液氨用于自身冷凍的液氨量也要盡量少一點(diǎn),這樣可以達(dá)到冰機(jī)開(kāi)啟量少,達(dá)到節(jié)約電耗的目的。
ⅢJD系統(tǒng)從下述方面進(jìn)行冷回收系統(tǒng)優(yōu)化。
(1)三級(jí)冷卻兩級(jí)分離的冷系統(tǒng)流程
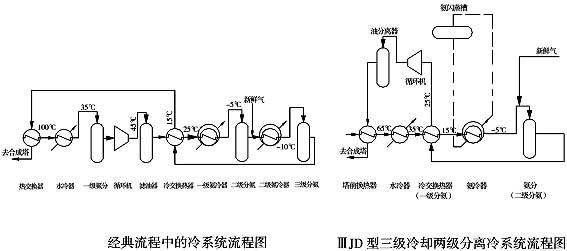
圖6 冷系統(tǒng)流程示意
一般的冷系統(tǒng)流程與ⅢJD冷系統(tǒng)流程示意見(jiàn)圖6。
從上述流程可以看到,傳統(tǒng)的流程采用了水冷后設(shè)氨分,并有兩級(jí)氨冷三級(jí)氨分的復(fù)雜系統(tǒng)。而ⅢJD的流程采用了十分簡(jiǎn)潔的冷系統(tǒng)流程——水冷一級(jí)冷卻后再進(jìn)入冷交進(jìn)行進(jìn)一步冷卻,分離;第三級(jí)冷卻為冷凍冷卻方式,這一級(jí)采用液氨蒸發(fā)冷卻合成氨循環(huán)氣,將氣相中未冷卻的氨進(jìn)一步冷卻,冷卻后再進(jìn)行冷凝,然后第二次分離。含有大量冷量的冷氣進(jìn)入冷交換器內(nèi)回收冷量后再入循環(huán)機(jī)。
這種流程的好處是在水冷后進(jìn)一步冷卻就可以在冷交下部將70%以上的液氨回收分離,降低了后續(xù)冷凍及分離的負(fù)荷,同時(shí),由于分離靠前,后續(xù)的液氨吸收冷量的問(wèn)題也解決了。另一方面也降低了冷系統(tǒng)的阻力。與經(jīng)典的流程比較,冷系統(tǒng)的液氨蒸發(fā)量下降近30%,出冷交換器冷氣的溫度上升10℃以上。
ⅢJD在低壓合成技術(shù)上,由于合成壓力較低,氨分離要求的循環(huán)氣溫度較低,為節(jié)約冷量,一般設(shè)兩級(jí)到三級(jí)的冷卻系統(tǒng),仍用二級(jí)分離方式達(dá)到盡量節(jié)約冷量的目的。
(2)高效冷卻器及冷熱交換設(shè)備
和“熱回收”系統(tǒng)一樣,“冷回收”系統(tǒng)照樣用了高效換熱技術(shù),設(shè)計(jì)了一個(gè)運(yùn)用高效螺紋管和特殊折流元件的冷交換器,將傳熱效率提高,減少了高壓容器的投資,收到了回收冷量好的效果。
同時(shí)也設(shè)計(jì)了一個(gè)傳熱效果好的氨冷卻器,采用了帶閃蒸槽的液氨蒸發(fā)方式,將換冷段設(shè)計(jì)成高效流動(dòng)型的冷換系統(tǒng)。同時(shí)提高了高壓容器的使用效率,提高了使用安全性能。
通過(guò)上述兩種措施,新的“冷回收”系統(tǒng)達(dá)到了設(shè)備配置最簡(jiǎn)單化,系統(tǒng)“冷回收”最大化的效果。目前運(yùn)行的幾十套大、中型ⅢJ合成系統(tǒng),均采用這種流程及設(shè)備的冷回收系統(tǒng)。通常都能降低入合成工段的冷量消耗,降低合成工段的液氨加入量,一般可達(dá)到自用液氨返用于冷系統(tǒng)量比傳統(tǒng)的流程及設(shè)備少100~200kg。同樣的氨加入量將會(huì)使進(jìn)口氨含量下降更多一點(diǎn);冷交換器的冷氣出口溫度高達(dá)22℃以上。
3.5 分離單元
ⅢJD系統(tǒng)的分離單元分為油、水分離器和氨分離器兩種類型,油、水分離主要是系統(tǒng)循環(huán)機(jī)及壓縮來(lái)新鮮氣的油、水及合成系統(tǒng)微量毒物的分離及凈化。氨的分離分為高溫部分的氨分離和低溫部分的氨分離,主要是指冷交下部的氨分離和氨冷后的氨分離。
新鮮氣的微量毒物及油、水的分離,ⅢJD系統(tǒng)主要采用分子篩系統(tǒng)來(lái)處理,當(dāng)分子篩系統(tǒng)處理的氣體達(dá)標(biāo)后,這部分新鮮氣可以直接補(bǔ)在合成塔進(jìn)口。這樣,可以減少合成系統(tǒng)循環(huán)量25%。但當(dāng)分子篩效果不好時(shí),我們?cè)O(shè)置了將補(bǔ)入氣補(bǔ)到“冷系統(tǒng)”的凈化方式,工程上常用兩種方式并舉,流程可以互換的方式來(lái)配置。
油分離器采用的為多級(jí)離心分離串超級(jí)過(guò)濾的方式來(lái)處理氣體。氨分離器在高溫分離段,主要采用螺旋管及螺旋流動(dòng)型折流元件,使液氨在換熱段邊冷卻邊順流,氨液滴長(zhǎng)大后再進(jìn)入離心分離段,再采用過(guò)濾分離方式來(lái)分離液氨。
低溫段氨的分離采用三級(jí)到四級(jí)離心分離、過(guò)濾分離及超濾分離組合的分離方式,這樣可達(dá)到在一定循環(huán)氣溫度下能分離液相氨90%的分離效果。大系統(tǒng)也采用了臥式氨分離器來(lái)集成分離冷系統(tǒng)出來(lái)的液氨。
采用這些設(shè)計(jì)方式,分離效果得到了提高,分離器的阻力降也比較小。
運(yùn)用上述設(shè)計(jì)思想及設(shè)計(jì)方法,我們?cè)O(shè)計(jì)了多套氨合成系統(tǒng),在全國(guó)很多廠家運(yùn)用,均收到了良好的效果,目前正在進(jìn)一步優(yōu)化系統(tǒng),使熱回收量更大、系統(tǒng)能力更大。
4 ⅢJD氨合成系統(tǒng)的推廣業(yè)績(jī)及達(dá)到的技術(shù)水平
按照上述設(shè)計(jì)思想,我們創(chuàng)造的ⅢJD型氨合成系統(tǒng)在全國(guó)大中型合成氨企業(yè)推廣面日益增大,1995年山東魯西化工股份有限公司采用我公司設(shè)計(jì)和制造的31.4MPa級(jí)的DN1200合成系統(tǒng),拉開(kāi)了大直徑合成塔研究和應(yīng)用的序幕,此后相繼開(kāi)發(fā)了DN1400、DN1600、DN1800、DN2000、DN2200系統(tǒng),近期又進(jìn)行了DN2800、DN3200、DN3400的低壓氨合成系統(tǒng)和二塔三塔串聯(lián)低壓及高壓氨合成系統(tǒng)的開(kāi)發(fā)。為我國(guó)合成氨自主技術(shù)的開(kāi)發(fā)作了大量前瞻性的工作。
開(kāi)發(fā)的DN1400合成氨系統(tǒng)在湖南大乘資氮集團(tuán)成功運(yùn)行近6年;DN1400系統(tǒng)還在江蘇昆山錦港實(shí)業(yè)有限公司、山西豐喜集團(tuán)臨猗分公司、江蘇新沂恒盛化工有限公司、山西天脊集團(tuán)晉城化工股份有限公司等廠投入運(yùn)行。公司開(kāi)發(fā)的DN1600氨合成系統(tǒng)最早的一套在湖南岳陽(yáng)天潤(rùn)化工股份有限公司(岳陽(yáng)化肥廠),已運(yùn)行近5年,相繼又有河南心連心化工有限公司(河南新鄉(xiāng)化肥廠)、河北邯鋼集團(tuán)化肥廠、福建三明化工總廠、山西晉成煤氣化有限責(zé)任公司、河南駿馬化工集團(tuán)公司化肥廠等廠采用DN1600氨合成系統(tǒng);開(kāi)發(fā)的DN1800氨合成系統(tǒng)在山東瑞星化學(xué)工業(yè)集團(tuán)公司于2003年底投入生產(chǎn),相繼有山東德齊龍化工有限公司三套的醇烴化配DN1800氨合成系統(tǒng)聯(lián)合工段投產(chǎn),江蘇新沂恒盛化工有限公司的18·30工程中的醇烴化及DN1800氨合成系統(tǒng)投產(chǎn),江蘇華昌化工有限公司的18·30工程中的醇烴化及DN1800氨合成系統(tǒng)投產(chǎn);開(kāi)發(fā)的DN2000氨合成技術(shù)在山東德州化肥廠、河南心連心化工有限公司、山東明水化肥廠等企業(yè)相繼投用;開(kāi)發(fā)的DN2200氨合成系統(tǒng)近期將在山東魯西化肥股份公司投入運(yùn)行。
基于我公司在合成系統(tǒng)技術(shù)的先進(jìn)性,2002年4月24~25日,中國(guó)氮肥工業(yè)協(xié)會(huì)組織全國(guó)合成氨方面的專家,對(duì)雙甲和醇烴化凈化工藝及合成氨技術(shù)進(jìn)行了針對(duì)山西臨猗現(xiàn)場(chǎng)的生產(chǎn)評(píng)議,評(píng)議認(rèn)為:“……ⅢJD氨合成系統(tǒng)及主要設(shè)備結(jié)構(gòu)均采用了優(yōu)化設(shè)計(jì),在國(guó)內(nèi)外處于領(lǐng)先水平,建議在氮肥行業(yè)推廣應(yīng)用。”
二十多年來(lái),ⅢJ系列氨合成技術(shù)在安淳人及廣大用戶的共同努力下,獲得多種獎(jiǎng)勵(lì)。技術(shù)也被列為國(guó)家級(jí)重大科技成果重點(diǎn)推廣項(xiàng)目。技術(shù)成果參加過(guò)維也納、吉隆坡國(guó)際新技術(shù)新產(chǎn)品展覽,獲國(guó)家級(jí)新產(chǎn)品稱號(hào)、獲1995年度國(guó)家科技進(jìn)步二等獎(jiǎng)(迄今為止,國(guó)內(nèi)合成塔內(nèi)件最高獎(jiǎng)項(xiàng))、中國(guó)專利技術(shù)金獎(jiǎng)、湖南省科技進(jìn)步一等獎(jiǎng)。
現(xiàn)在有400多家合成氨廠使用該技術(shù)及內(nèi)件,F(xiàn)選擇一部分大型塔的推廣運(yùn)行實(shí)例,來(lái)說(shuō)明和驗(yàn)證產(chǎn)品及系統(tǒng)運(yùn)行情況。
河南心連心化工有限公司 該廠2003年新投入一套150 kt/a合成氨裝置,合成工段及凈化精制工段采用了我公司的ⅢJD系統(tǒng)及醇烴化凈化精制工藝來(lái)實(shí)現(xiàn),裝置于2003年8開(kāi)車,合成氨生產(chǎn)500t/d,甲醇生產(chǎn)180t,系統(tǒng)壓力只有26MPa。開(kāi)工后,企業(yè)每天比原來(lái)系統(tǒng)天多創(chuàng)利潤(rùn)20~25萬(wàn)元。今年8月份,該廠230 kt/a總氨的氨合成系統(tǒng)及醇烴化凈化系統(tǒng)也一次開(kāi)車成功,這是我公司又一次與心連心化工公司的技術(shù)合作,本次設(shè)計(jì)采用了一套DN2000氨合成系統(tǒng),這也是國(guó)際國(guó)內(nèi)31.4 MPa級(jí)最大的氨合成系統(tǒng)。運(yùn)行后,達(dá)到了日合成氨產(chǎn)量500t/d,甲醇產(chǎn)量180t/天的水平,系統(tǒng)運(yùn)行壓力僅18 MPa,目前正在進(jìn)行大負(fù)荷生產(chǎn)調(diào)試,近期將達(dá)到日產(chǎn)700 t合成氨,系統(tǒng)壓力僅23MPa,為我國(guó)特色的合成氨系統(tǒng)創(chuàng)造新的業(yè)績(jī)。
山東瑞星化工集團(tuán)公司 公司現(xiàn)有合成氨能力400 kt,曾于1996、1998年使用我公司的DN1200、 DN800ⅢJ-99氨合成系統(tǒng)各一套,于2003年底在400 kt/a合成氨技術(shù)改造中,率先采用了我公司的一套DN1800氨合成系統(tǒng),于2003年底投產(chǎn)。投用之初,系統(tǒng)每天產(chǎn)合成氨620t,系統(tǒng)壓力只有24MPa。目前運(yùn)行近三年了,后串入一個(gè)合成塔彌補(bǔ)合成塔上部催化劑老化的不足,系統(tǒng)可以開(kāi)到合成氨產(chǎn)量700t以上,整個(gè)分離系統(tǒng)尚能達(dá)到產(chǎn)量要求,為我公司設(shè)計(jì)的系統(tǒng)進(jìn)一步挖潛改造提供了成功的經(jīng)驗(yàn)。
江蘇華昌化工有限公司 這個(gè)廠用了我公司三套氨合成及醇烴化系統(tǒng),一套DN1600氨合成系統(tǒng)。開(kāi)車近三年了,目前合成氨產(chǎn)量達(dá)到了600t/d以上,系統(tǒng)壓力僅28MPa,達(dá)到了穩(wěn)定、高效、節(jié)能運(yùn)行的效果。
湖南岳陽(yáng)天潤(rùn)化工股份有限公司 該公司目前擁有合成氨生產(chǎn)能力180 kt/a。2000年初,投用了我公司一套DN1600氨合成系統(tǒng),此系統(tǒng)為ⅢJD系統(tǒng)的第一套,目前合成氨產(chǎn)量達(dá)450t/d,系統(tǒng)壓力只有21MPa,到目前為止催化劑使用約6年。
山西晉城煤化工有限責(zé)任公司 該公司進(jìn)行220 kt/a合成氨工程擴(kuò)建時(shí),采用了我公司的醇烴化工藝及氨合成工藝,于2002年12月投產(chǎn)了一套DN1600ⅢJD的氨合成系統(tǒng),目前日產(chǎn)合成氨6000t,系統(tǒng)壓力只有27MPa。
湖南大乘資氮集團(tuán)有限公司 這是最早采用我公司ⅢJD氨合成系統(tǒng)的廠家,目前一套DN1200和一套DN1400氨合成系統(tǒng),每天產(chǎn)氨和醇共計(jì)850t。綜合經(jīng)濟(jì)效益十分顯著。
除此之外,還有山東德州化肥廠、山東魯西化工股份限公司、山東明水化肥廠、河南開(kāi)封晉開(kāi)化工公司、山東德齊龍化工有限公司、邯鋼集團(tuán)化肥廠、福建三明化工總廠、河南距馬店化工總廠、江蘇昆山錦港實(shí)業(yè)集團(tuán)公司、江蘇華爾潤(rùn)集團(tuán)公司、江蘇張家港錦港實(shí)業(yè)公司、山西豐喜集團(tuán)臨猗分公司、江蘇新沂恒盛化工有限公司、天脊集團(tuán)晉城化工股份有限公司等廠先后采用了我公司ⅢJD型氨合成系統(tǒng)。
我公司的ⅢJD型φ1200~φ2200 mm氨合成系統(tǒng)及氨塔內(nèi)件在全國(guó)的應(yīng)用是十分廣泛,占合成氨廠塔型中的30%以上,占上述直徑塔型的70%以上。
5 結(jié)束語(yǔ)
ⅢJD型氨合成塔系統(tǒng)及合成塔技術(shù)為我國(guó)自行設(shè)計(jì),具有自主知識(shí)產(chǎn)權(quán)、適應(yīng)我國(guó)國(guó)情的合成氨技術(shù),湖南安淳公司從事大型化合成系統(tǒng)技術(shù)研究及系統(tǒng)開(kāi)發(fā)近20年,運(yùn)用了多項(xiàng)國(guó)家專利技術(shù),創(chuàng)造了節(jié)能效果好的大型化系統(tǒng),為合成氨產(chǎn)業(yè)的國(guó)產(chǎn)化走出了一條新路。采用了現(xiàn)代化的設(shè)計(jì)理念及新材料、新的技術(shù)進(jìn)行設(shè)計(jì)。隨著更大型化的合成系統(tǒng)投產(chǎn),將進(jìn)一步檢驗(yàn)安淳公司的技術(shù)水平及技術(shù)成果,為我國(guó)合成氨的國(guó)產(chǎn)化提供成功的經(jīng)驗(yàn)。

元豐資訊:
氮肥與甲醇技術(shù)網(wǎng)
尿素網(wǎng)
造氣網(wǎng)
二甲醚網(wǎng)
尿素世界網(wǎng) (英文版)
產(chǎn)品技術(shù)庫(kù)
VIP商務(wù)俱樂(lè)部
化工論壇
QQ群大聯(lián)盟
| 會(huì)員登錄 |
網(wǎng)站地圖 |
意見(jiàn)反饋 |
關(guān)于我們 |
聯(lián)系我們 |
網(wǎng)站指南 |
法律申明 |
保護(hù)隱私權(quán) |
致作者 |
Copyright © 2008-2010 中國(guó)氮肥與甲醇技術(shù)網(wǎng) 版權(quán)所有 蜀ICP備05031754號(hào) E-mail:yf116@vip.163.com
地址:成都市青白江區(qū)怡湖芳鄰18棟8號(hào) 電話:028-83667786,83667576,89309098 傳真:028-83667578