如今,減少化肥裝置的排放物變得越來越為重要。隨著國際社會對環(huán)境受到人為干擾影響的意識的不斷提高,各種排放物受到日益關注,并正在努力將排放量減少到最低限度。這不僅針對西歐,而且也針對世界上的所有其他地方。
對于尿素項目,我們要求提供可用的最佳減排技術,然而,各個項目的減排形式可能有所不同。多年來,斯塔米卡邦已經實現了用于控制各種排放的許多不同設計方案。然而,具體項目的最終設計取決于地方部門的適用要求及最終客戶的理念。此外,最終設計方案的選擇,還應考慮某些經濟可行性。到目前為止,我們還沒有將所有排放減少到最低限度的統(tǒng)一設計方案。
本文介紹了科威特石化工業(yè)公司(PIC)氨零排放項目的設計。
2 科威特石化工業(yè)公司氨零排放項目
科威特石化工業(yè)公司目前正在運營兩臺氨裝置和三臺尿素裝置進行液氨和大顆粒尿素生產。氨裝置和尿素裝置的總造粒能力分別為1880t/d和3150t/d。氨裝置基于M/s Haldor Topsoe公司的技術,尿素裝置則基于斯塔米卡邦汽提技術。第一臺氨裝置/尿素裝置于1966年試運行,1970年,增加另外兩臺氨裝置和兩臺尿素裝置。1984年,安裝另一臺氨裝置后,科威特石化工業(yè)公司的合成氨裝置和尿素裝置的生產能力成為中東之最。
科威特石化工業(yè)公司一向非常積極地與國際社會合作,以滿足或超過各項環(huán)境要求。該機構的目標是總是優(yōu)于任何強制性要求。
對從尿素裝置緊急減壓系統(tǒng)(安全閥或爆破片)排出的含氨工藝氣體通常采用直接排放至大氣的方法來處理。這是此類設施的習慣做法,至今仍然是全世界許多地方的習慣做法。盡管可以安全方式將含氨工藝氣體直接排放至大氣,但這會對裝置附近的環(huán)境造成相當大的污染。作為一個有社會責任的企業(yè)公民,科威特石化工業(yè)公司決定通過實施“氨零排放項目”消除PIC聯合裝置的內部和外部氨污染,以實現零排放。
3 火炬燃燒來自安全減壓裝置的工藝蒸氣
對吸收利弊和火炬系統(tǒng)(用于處理緊急安全減壓裝置排放的NH3-CO2-H2O混合物)進行深入分析后,火炬燃燒被選為適當的技術。
設計包括以下步驟:
• 在設施內設計和實施主要氨源收集系統(tǒng);
• 以安全閥替代爆破片;
• 審查和分析設施的減壓裝置和氨源,以確定將氨釋放到收集系統(tǒng)內來代替排放至大氣中的影響。
• 分析可能性減壓情景,以確定減壓系統(tǒng)的尺寸。
• 出于液壓和機械考慮,分析收集網絡。
3.1 A裝置的火炬燃燒工藝蒸
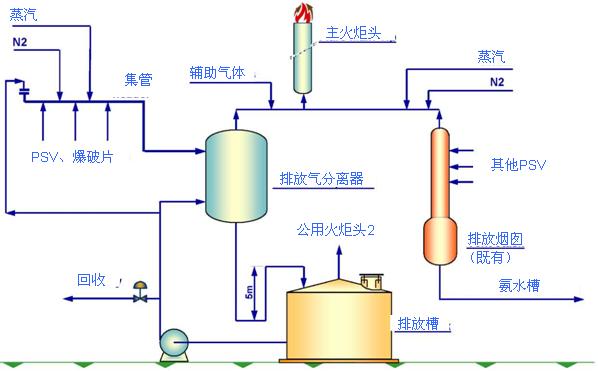
圖1
如果安全閥排氣,閃蒸液或蒸氣進入排氣分離器。如果有液體,液體將與蒸氣分離,然后排入排放槽。含氨蒸氣與輔助氣體混合后被送至主火炬頭,以增加其熱值,從而通過燃燒幾乎完全消除氨。排氣分離器是具有切向進液口的旋風式分離器,專為高壓汽提塔的管破裂情況設計。
通過5m液體密封將來自排氣分離器的液體排至排放槽,以防止蒸氣進入排放槽。設計火炬系統(tǒng)和互連管道,使得排氣分離器內的最大壓力不超過0.3巴。由于過壓,來自排放氣分離器的液體會在常壓排放槽內閃蒸,蒸氣被引入專用公用火炬頭2。公用火炬的壓降使得不超過排放槽的機械設計壓力。然而,為了防止排放槽受到可能性過壓,在槽頂設置人孔水封。
排放槽的容量設計為容納完全合成排放。這有可能發(fā)生在高壓換熱器的管破裂處。
合成液體閃光至大氣壓力時,其溫度會大幅下降,然后結晶。為了避免分離器至排放槽的出液口管線堵塞,且使排氣系統(tǒng)無固體甲銨,應維持連續(xù)水循環(huán)。連續(xù)水循環(huán)作為流至排放槽的尿素/甲銨溶液的稀釋劑。
排放槽的初始水量適應于液體合成總量。
確保在完全合成排放后,排放槽內沒有甲銨結晶。
如果排放槽受尿素和/或甲銨污染,可通過將液體送至精餾塔在工藝過程中回收液體。在回收過程中,應通過提供新的蒸汽冷凝液維持排放槽的最低液位。圖1說明A裝置的系統(tǒng)設計方案。既有排放煙囪的出口與主火炬總管連接,合成安全閥則與排氣分離器連接。
3.2 B裝置的火炬燃燒工藝蒸氣
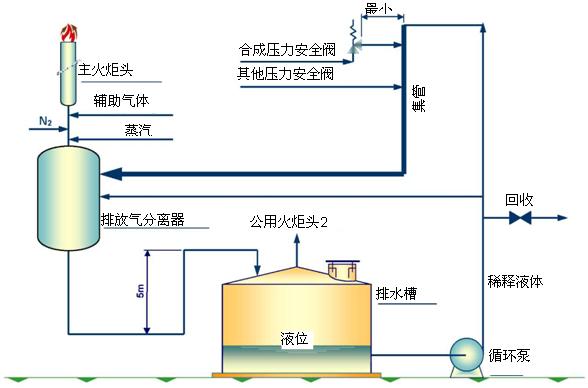
圖2
從圖2可見,來自該裝置的既有安全閥的所有排氣管線現在均改線并連接至新的集管。在原設計中,所有工藝安全閥(合成壓力安全閥和爆破片除外)均與排放煙囪連接。排放煙囪的底部處于地面高度,因此,與A裝置相比,B裝置沒有流至氨水槽的重力溢流。如果甲銨泵上的安全閥在較長一段時間內排氣,則可能發(fā)生煙囪過量灌裝并因此使火炬帶有液體的情況。詳細檢查也表明既有排放煙囪過量灌裝時,其結構并不可靠。因此,決定取消既有排放煙囪,并將所有安全閥改線至集管,包括替代爆破片的新安全閥。3.3 火炬系統(tǒng)吹掃
尿素合成塔的安全閥和合成爆破片通常不與排放煙囪連接,但和短排氣管連接。因為安全閥可能泄漏,所以該設計主要是為了確保安全閥出口不會被固體甲銨阻塞。短排氣管還方便進行目視檢查。
在新的設計方案中,所有安全閥均與集管連接。
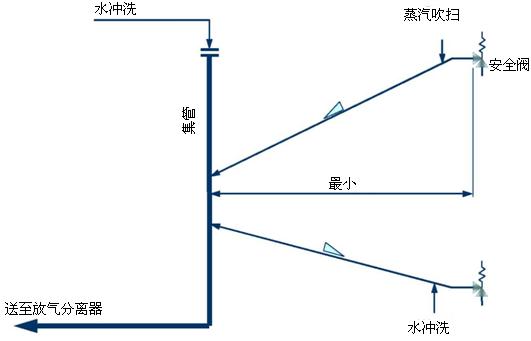
圖3
為了確保排氣系統(tǒng)沒有固體甲銨,所有安全閥均具有吹掃系統(tǒng),參見圖3。用水清洗向上傾斜的排氣管道,用蒸汽吹掃向下傾斜的排氣管道。所有吹掃的分布式控制系統(tǒng)(DCS)內均具有流量計和高優(yōu)先級低流量報警器。
為了消除與通過壓力安全閥相關的問題,通過注入輔助低壓蒸汽將火炬總管的溫度(靠近火炬煙囪入口點測量)維持在100℃。通過溫度控制回路調節(jié)輔助蒸汽的注入。火炬頭還完全蒸汽伴熱和隔熱,以最大程度減少低壓蒸汽消耗量。
為了安全起見,應避免氧氣(空氣)進入火炬系統(tǒng)。為了消除火炬總管內形成爆炸性混合物的可能性,火炬頭內的最高允許氧含量為8 vol.%?赏ㄟ^在每個火炬頭內安裝吹掃密封件實現。氮氣用作吹掃介質。
3.4 液氨/氨蒸氣的火炬燃燒
正如所知,液氨和水的親和力均較強。向水中突然釋放液氨會產生巨大的壓力波。因此,為了保護排放槽,應以不同于NH3-CO2-H2O混合物排放工藝安全閥的方式處理純液氨/氨蒸氣排氣安全閥。
科威特石化工業(yè)公司目前有以下安全閥:
• 高壓氨泵上的安全閥;
• 造粒裝置的氨制冷裝置上的安全閥;
• 高壓氨加熱器上的安全閥。
如果上述安全閥排氣,安全閥下游只有部分氨會蒸發(fā),大部分氨會冷卻至-33℃。蒸發(fā)所有氨所需的時間取決于隔熱溫度和環(huán)境溫度。
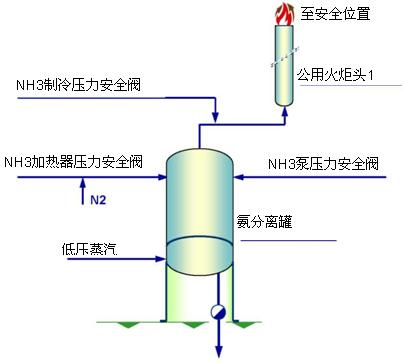
圖4
為了避免液氨帶入公用火炬頭1,并加速液氨蒸發(fā),來自安全閥的排氣管道連接至加熱氨分離罐。考慮到每種排氣情況的液體滯留,已經對分離罐的容積進行了優(yōu)化。然而,為了搶先過量灌裝分離罐和火炬總管,采用聯鎖裝置切斷送入火炬系統(tǒng)公用火炬頭1的氨,火炬頭1不需要輔助氣體。
3.5 火炬燃燒系統(tǒng)總體布置
對于兩種裝置,火炬均安裝在不再使用的造粒塔頂部。主火炬頭使用天然氣作為輔助氣體,用以燃燒來自排氣分離器的排放氣體。一個公用火炬頭用于來自液氨系統(tǒng)的排放氣體,一個公用火炬頭用于排放槽的排放氣體。
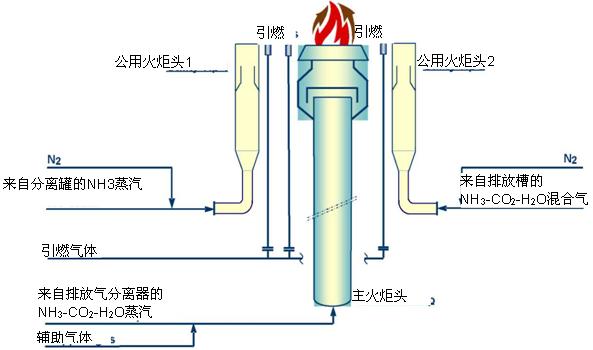
圖5
3.6 設計和安全方面應特別注意與火炬系統(tǒng)設計和安裝有關的幾個安全方面:
• 設計應確保送至火炬的排放氣體中沒有氧氣。為了避免氧氣進入火炬頭,應通過蒸汽吹掃將系統(tǒng)保持在100℃以上,蒸汽不僅用于惰化,而且用于加熱系統(tǒng),以防止結晶;鹁婵偣芎突鹁鏌焽杈羝闊岷透魺。此外,還將氮氣注入火炬系統(tǒng),使安裝在火炬頭處的整個密封件維持正向惰性氣體流。
• 在尿素裝置中引用天然氣時,需要采取具體措施:
* 應避免受尿素裝置中的其他介質污染;
* 對火炬區(qū)域進行分區(qū),隨后使設備符合出廠要求;
* 必須考慮散熱強度。
• 需要使用可靠的傳感器來檢測主火炬系統(tǒng)內是否存在氨,通過聯鎖輔助氣體供氣觸發(fā)傳感器。
• 應在主火炬頭火炬總管內安裝天然氣檢測器,以監(jiān)控火炬頭內是否存在天然氣。
• 廣泛的可能性組成。
尿素裝置的排放氣體的氨濃度和量差異很大,需要對火炬的正確設計進行徹底評估。
• 在所有情況下,為了限制管道受力過度,且最大程度減少摩擦壓降,至集管的連接呈Y型連接。
4. 工藝槽上的吸收塔
科威特石化工業(yè)公司的許多常壓工藝槽均可用于尿素溶液和氨水的中間儲存。出于靈活性考慮,這些工藝槽均與兩個裝置連接。常見做法是,在造粒機清洗過程中,尿素產品臨時儲存在工藝槽內。造粒設備通常出現產能過剩,這樣,在造粒機重新開啟時可以回收工藝槽內儲存的溶液。
盡管將尿素溶液儲存在工藝槽內,由于工藝槽排氣(液位持續(xù)上升),尿素水解為尿素、二氧化碳和氨,以及形成雙縮脲,氨排放不可避免。
已探討了火炬燃燒這些蒸氣的可能性,但因以下原因而遭到拒絕:
• 部分工藝槽遠離火炬的擬議位置,因此管線較長,必須穿過道路等障礙。
• 許多工藝槽的機械設計壓力僅限于150mm H2O,低于火炬的所需背壓。
• 由于工藝槽的氨蒸氣排放因裝置故障和/或造粒裝置停機過程中尿素溶液轉移至工藝槽而幾乎總是持續(xù)不斷,安裝火炬來消除氨是沒有意義的建議。
因此,決定設計“低壓降”吸收塔來避免任何氨排放到大氣中。
4.1 離線尿素儲罐
如上文所述,在尿素裝置后端工段出現故障和清洗造粒機期間儲存尿素溶液時,因水解和排氣而出現氨排放。為了制定吸收塔設計基礎,進行動態(tài)模擬來計算工藝槽的氨排放量。因為情況隨時間變化,所以計算相當復雜。
為了進行設計,設置了以下設計基礎:
• 儲罐容積為650m3;
• 初始溶液溫度為100℃;
• 絕熱條件(儲罐不釋放熱量)。
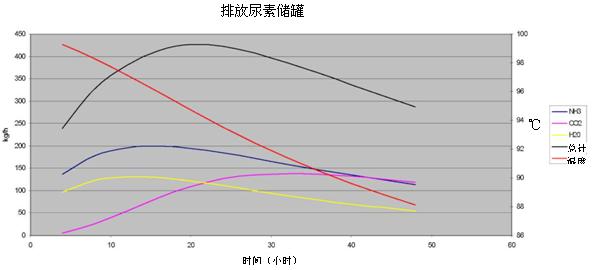
圖6
從圖6可見,吸熱水解反應使溶液溫度連續(xù)降低,從而降低反應速度。由于含尿素、水、二氧化碳和氨的混合物的共沸特性,由于時間的作用,儲罐的排放量達到最大。儲存約15小時后,氨排放量通常達到最大。參見圖7,由于儲罐內的最大容許壓力,吸收塔系統(tǒng)的設計是一項艱巨的任務。預計儲罐具有在150mm H2O過壓時破裂的水封。
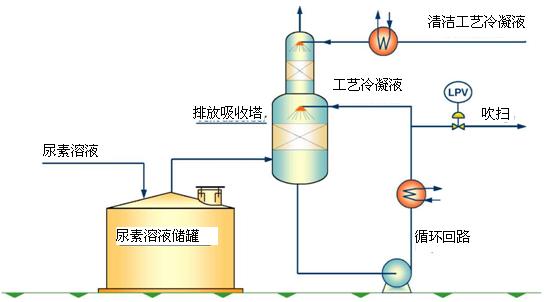
圖7
通過選擇低壓降填料和采用吸收塔設計,我們成功地在吸收塔系統(tǒng)中實現35mm H2O的最大壓降(設計負荷下)。設計負荷下的預計氨排放量為0.0 kg/h。該吸收塔系統(tǒng)僅在造粒清洗和儲罐回收過程中運行。
4.2 在線尿素儲罐
在工藝故障期間,不再維持閃蒸罐內的真空壓力,導致尿素儲罐氨排放。尤其是汽提效率降低時,閃蒸罐廢氣的氨蒸氣壓力變大,因此,很難在負壓下冷凝蒸汽。閃蒸罐內的液體壓力高于負壓時,常壓儲罐內出現閃蒸,導致氨排放。
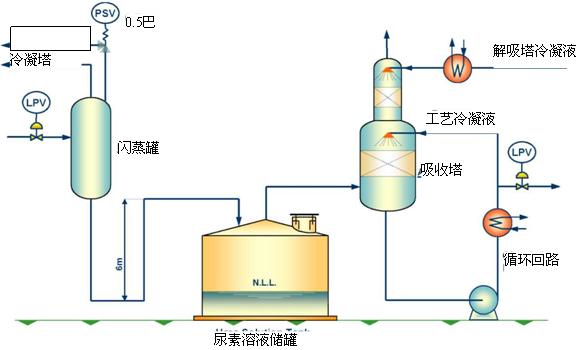
圖8
吸收塔的設計基礎是完全打開精餾塔出液口的液位控制閥(空氣故障時打開)。在這種情況下,PIC不允許發(fā)生儲罐水封破裂。為了限制進入儲罐的最大蒸氣量,將設定壓力為0.5巴的安全閥安裝在閃蒸罐上。通過給閃蒸罐出液口到尿素儲罐提供6m液封,蒸氣不可能直接進入儲罐。通過閃蒸液將儲罐的最大蒸氣壓力限制為0.5巴至大氣壓。吸收后,至大氣的氨排放量可忽略不計。
5 結 論
科威特石化工業(yè)公司氨零排放項目是如何利用火炬和/或吸收塔以可控方式吸收和處理尿素裝置的所有連續(xù)和間斷氨排放的好例子。應了解,正如我們在此論文中曾試圖說明的一樣,不同系統(tǒng)的設計是相當復雜的問題。
在本項目開始時,必須明確當地法定部門和裝置負責人的要求。在設計開發(fā)過程中,為了明確需要什么,及調整對現階段遇到的不同問題的意見,要求有關各方定期召開會議。所需壽命周期成本也是這些會議中要考慮的問題。
科威特石化工業(yè)公司氨零排放項目證明火炬燃燒是處理或消除發(fā)生裝置故障(不干擾鄰近裝置)時排放的氨的適當技術。